By Sursha Wu
质量管理是什么?
质量管理(Quality Management),是企业确保产品或服务能持续符合顾客需求与法规标准所进行的核心活动。无论是哪种行业,『做好质量管理』始终是提升顾客信任、降低运营风险,以及推动企业稳健成长的关键。
以制造业为例,质量管理通常着重于产品规格的一致性与生产流程的稳定性。传统的质量管理方法,即使在数位化程度不高的情况下仍能发挥一定成效,但在效率、弹性以及数据分析能力上存在明显限制。
随着生产日益复杂、跨厂甚至跨国协作成为常态,制造商逐渐意识到,唯有导入更进阶的质量管理系统,才能提升管理效率、降低人力成本,减少对现场经验的高度依赖,并实现更即时、主动的质量管理。
质量管理的 3 个重点
1. 完善制程质量管理,预防胜于检验
在制造业中,过程内质量管制(IPQC)扮演关键角色,其核心精神是『及早发现、立即修正』。比起事后检验,更重要的是在问题还小、还能控制的阶段就将它解决,避免错误扩散到最终成品。
只要在产线上能发现问题,马上检修,甚至都不需要费用。可是一旦这个东西放到市场上面,费用都很吓人。
── 电动汽机车制造商的智慧制造系统及解决方案处长
案例解析:德国豪华汽车品牌的召回风暴
德国某知名豪华汽车品牌于 2022 年内部就曾侦测到煞车系统异常。瑕疵原因来自供应商的人工组装作业未确实清洁电路板,进一步损害煞车系统,影响车辆安全。
此外,因未能及时在制程端发现错误,导致同样的异常生产存在产线长达 2 年,最终累积超过 150 万辆车辆被召回,维修与处理成本预估高达 10 亿欧元。严重的是,最终管理层仍无法肯定问题车辆皆已被回收,导致顾客与经销商信心大幅下降,媒体与市场也纷纷质疑该企业的质量控管与供应链监督能力,导致公司股价重挫近 28%。
—— News reference: 彭博社(Bloomberg)Sep. 16. 2024
这起事件凸显了制程质量管理与生产履历建立的关键性:
- 过程控管失效的代价高昂:一旦质量控管机制失灵,不仅将承受巨额财务损失,还可能动摇多年累积的品牌信任。
- 高安全性产业风险更高:在汽车、医疗、航空等高度仰赖安全性的产业中,质量问题可能引发连锁效应,冲击整体市场声誉,甚至威胁企业存续。
- 制程防错防呆是关键:导入预防性的制程管理与即时异常追踪机制,能减少事后追溯补救的巨额成本。
- 建立生产履历有助于问责与追溯:完整的生产纪录有助于快速厘清肇因与追溯异常产品,提升应变效率。
2. 透过方法论,持续改善作业流程
有效的质量管理强调持续改善。透过导入 PDCA、FMEA、六标准差等质量方法论,企业能系统性地辨识流程中的风险与缺陷,针对问题根本原因提出改善行动,进而提升产品一致性与生产效率。
3. TQM 全面质量管理,建立全员质量文化
全面质量管理(Total Quality Management, TQM)强调质量透过跨部门协作、持续训练、制度化的问题回报与改善流程,建立起从上到下的质量文化。当质量意识成为组织文化的一部分,问题能够在第一时间被发现与回应,整体营运也能更具韧性与竞争力。
质量管理的 5 种工具
透过有逻辑、有步骤的方法工具,企业可以更有效率地找出问题根源、建立可追踪的改善机制,最终实现整体质量与良率的上升。
1. PDCA 循环
PDCA 循环(PDCA Cycle),即计划(Plan)、执行(Do)、检查(Check)、行动(Act)。最早由美国著名管理学家爱德华兹·戴明(Edwards Deming)于 20 世纪提出的系统化质量管理概念。
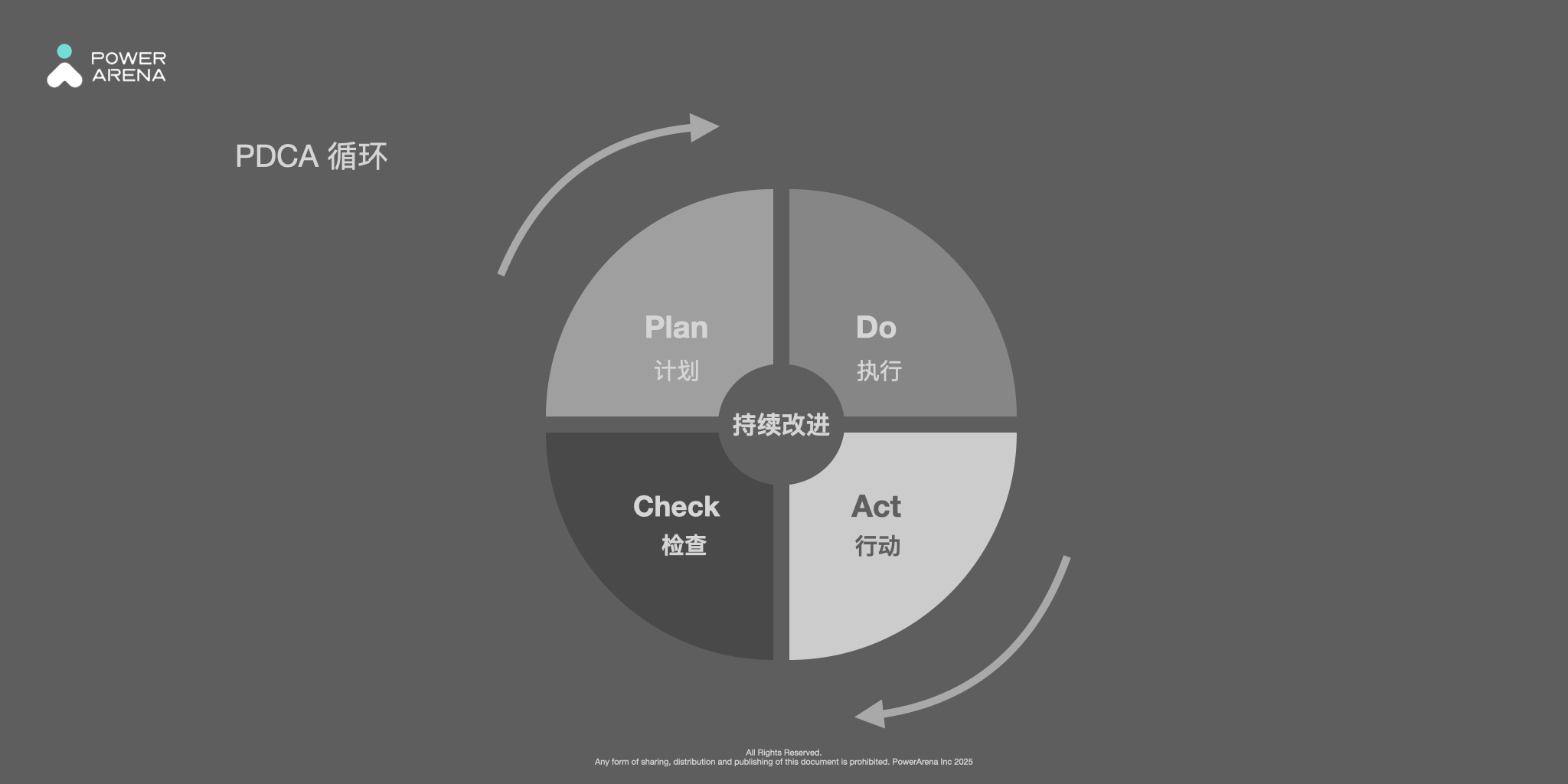
透过 PDCA 循环方法,持续改进作业流程,提升质量。
完成一次流程之后,以前次结果为基础,再建立下一个目标进行循环。直至达成质量管理目标。
2. FMEA 失效模式与效应分析
FMEA(Failure Mode and Effects Analysis)是一种系统化的预防性工具,广泛应用于产品设计与制造流程中,目的是在工厂投入大量生产前,提前辨识潜在失效模式,并评估其对产品与系统的影响,进而订出处理优先顺序与改善对策,避免不良品流入市场、造成召回、售后维修与品牌损害等高昂代价。
场域应用案例:
一家电动车龙头厂商,为提升车体组装的可靠性与安全性,导入 FMEA 分析工具,针对关键制程进行风险评估。管理团队先逐一列出潜在的失效模式,并透过 RPN(风险优先数)计算来排序处理优先级。
深入调查发现,造成失效的原因包括人工检测效率低落与操作错误频繁,因此企业决定导入 AI 视觉检测系统,提升异常辨识准确率,并结合 SOP 改进训练,降低发生度与侦测难度。
3. CLCA 闭循环修正措施
CLCA (Close Loop Corrective Action)是一套强调『发现问题、追查根因、执行改善并验证是否有效』的闭环质量管理流程,最早由 DELL 公司导入并广泛应用于制造业。它的核心目的在于防止问题再次发生,确保每次异常都能真正被解决、留下可复用的改善经验。
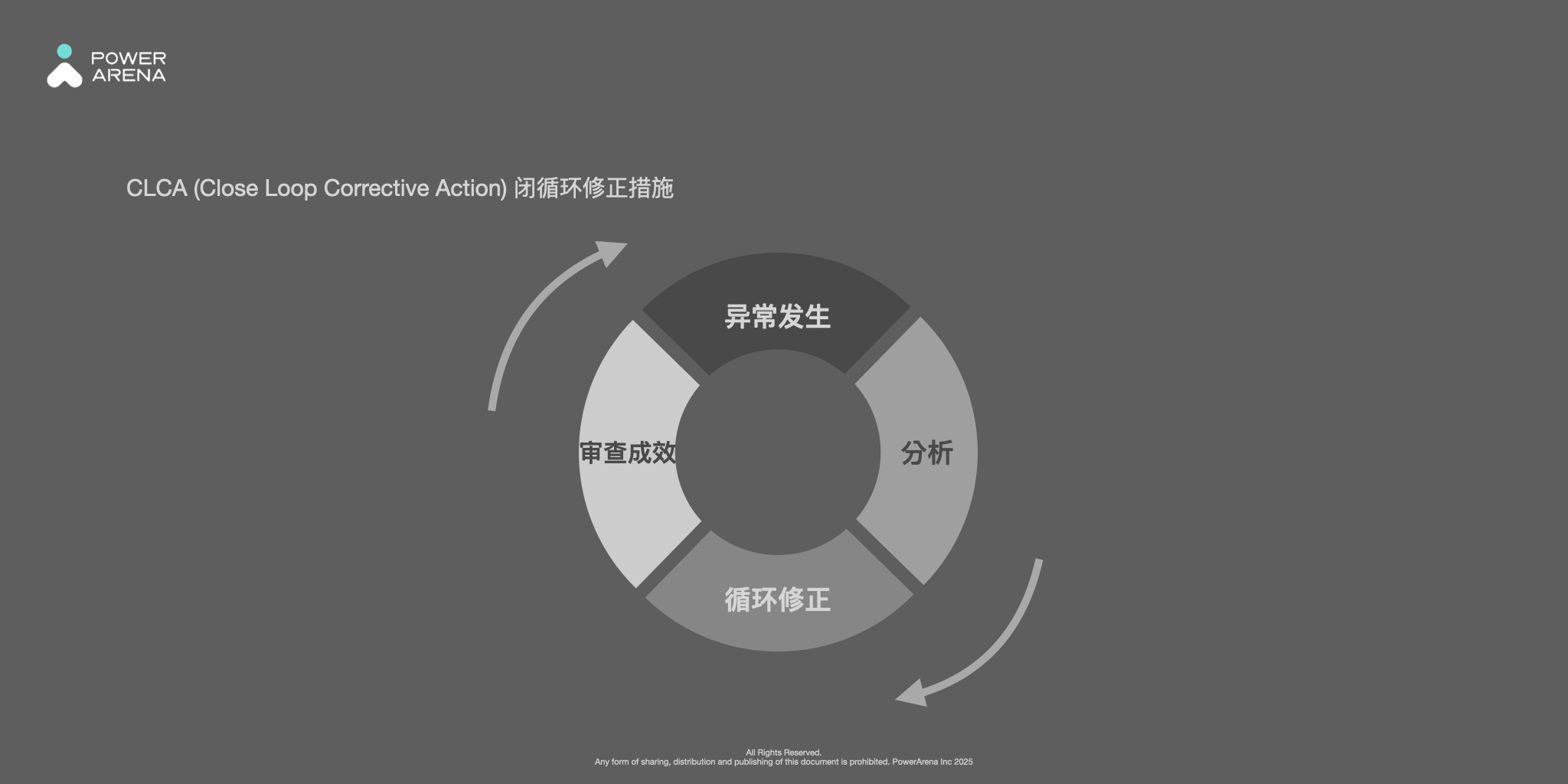
CLCA (Close Loop Corrective Action) 闭循环修正措施。
工厂例子是,某条产线长期处于线平衡异常的状态,透过生产影像纪录回溯问题后,迅速找出了根本原因——设备异常与参数设定错误。针对这一肇因,管理层立刻制定了改进方案。未来,其他管理人员可以直接参考这份改进方案,快速掌握解决问题的步骤,减少沟通成本。
.001-1.jpeg)
工厂利用 HOP 人因作业平台中的 CLCA 功能,完整保留产线改善纪录。
4. 六标准差 Six Sigma
六标准差是一套以数据为基础的质量改善方法,透过 DMAIC(定义、测量、分析、改善、控制)五步骤,系统性找出制程变异的根本原因并加以改善。其目标是将缺陷率降至百万分之 3.4 以下,确保产品一致性与流程稳定。广泛应用于电子、汽车、医疗等对质量要求极高的产业。
5. 质量管理系统(如 ISO 9001)
ISO 9001 是国际通用的质量管理标准,协助企业建立标准化流程、强化内部控管,并落实以顾客为中心、持续改善与风险导向管理。通过认证代表企业具备稳定的质量体系;对客户而言,ISO 认证是一种专业信任背书,有助于降低合作风险与建立长期合作关系。
资料来源:https://www.isolution.com.tw/what-is-iso9001/
质量管理的各职务分类与内容
以下是制造业中常见的质量管理职务分类及其工作内容:
- 质量保证(QA, Quality Assurance)
- 质量管制(QC, Quality Control)
- 制程质量工程师(QE, In-Process Quality Engineer)
- 供应商质量管理(SQE, Supplier Quality Engineer)
- 质量数据与系统管理(QMS / Data Analyst)
随着智慧工厂与制造数位化的发展,大型企业开始出现更专职的「质量数据分析师」与「系统管理人员」角色。他们主要负责企业内部的质量管理系统(QMS)维运,并整合来自现场的各类检验数据,进行分析与视觉化呈现,让管理层能以数据为依据进行决策。
具备技术背景的分析师,可能进一步参与 AI 模型的开发与导入,用于建立质量预测模型、异常预警系统等应用。
制造业在面临质量管理的 5 个问题
1. 生产 SOP 执行不足
许多产线虽已建立了生产 SOP,但这些规范往往未能充分考虑现场实际操作的习惯、环境限制,或是流程中可能出现的变异情境。导致 SOP 虽存在,却难以在实务中完全落实,可能直接影响产品质量。
此外,即使工厂已导入 SCADA、IoT 或 MES 等系统,虽然能有效搜集设备层级的数据,却普遍难以即时掌握人工作业流程中的异常状况。资讯落差使得产线真正的瓶颈容易被忽略。
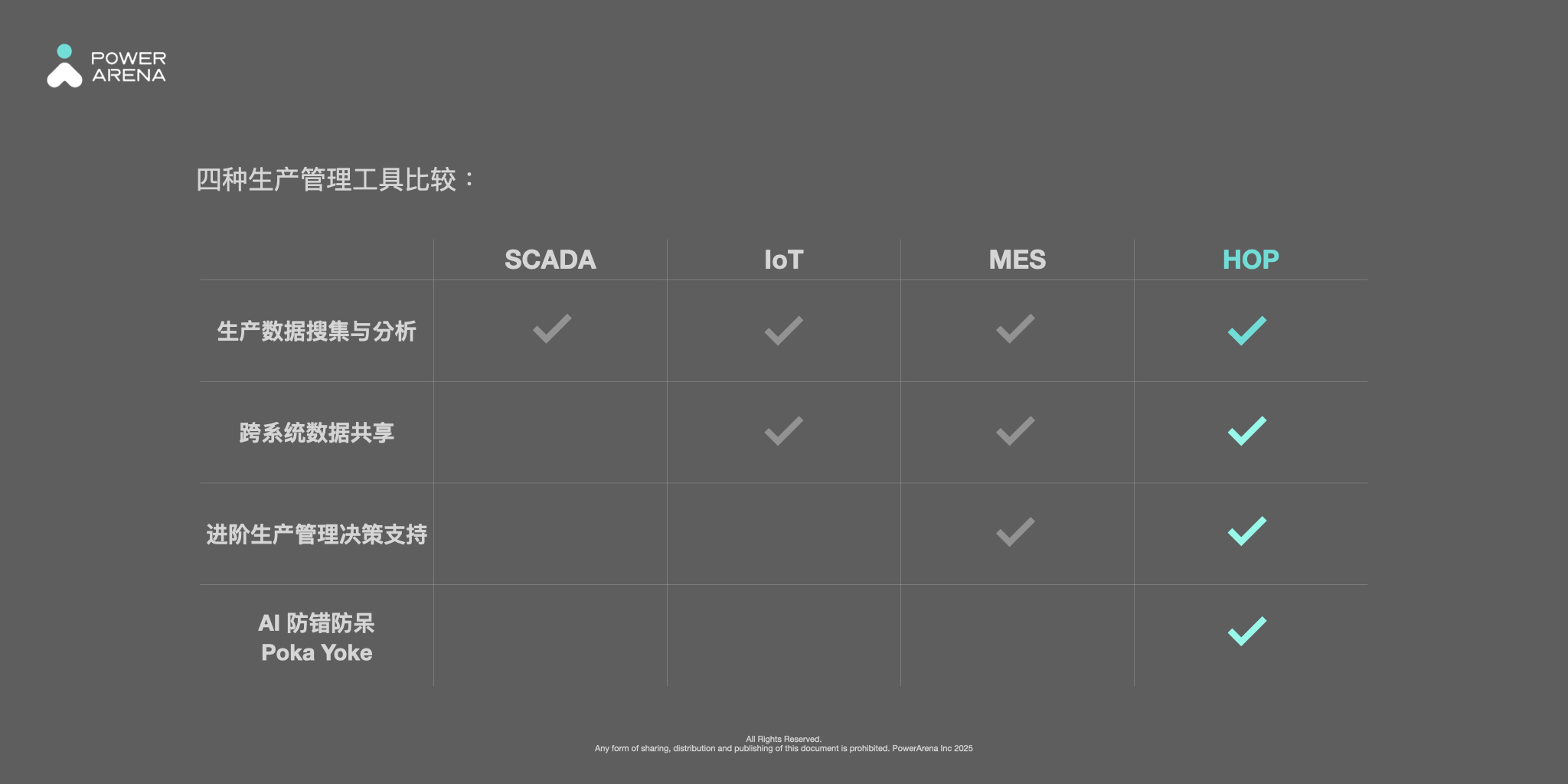
HOP 人因作业平台,能够自动搜集与分析生产数据的系统,并能以 AI 视觉建立防错防呆机制。
2. 难以在制程当下排除瑕疵
在许多工厂中,制程瑕疵若未能在当下即时被发现,往往会因为下一站料件的覆盖或装配而被掩盖,难以在品检端检出,而是在市场端客诉时才曝光。
另一方面,许多工厂现今也面临高离职率的问题,新进员工对操作流程不熟悉,极易产生质量偏差。对于第一线的管理者来说,即使再强化教育训练,也难以持续监控每位员工的操作细节。
当老手与新手混在线上作业时,生产效率、生产质量常受到影响。仅依赖最终品检(Final Quality Control)筛出不良品,必会增加返工成本与材料浪费,提高整体生产成本。
HOP 人因作业平台透过 AI 视觉技术,协助现场人员即时追踪作业员的操作行为,确保每个步骤皆符合 SOP。系统于产线部署摄影机,不仅记录整个生产过程,更能在制程发生的当下即时判断作业是否偏离标准,主动识别异常。
3. 无法全面生产资讯搜集与分析
在传统管理模式下,工业工程师必须投入大量时间进行人工观察与记录,但这样的方式无法覆盖所有时段,也难以精确掌握像是作业员离岗、操作空档等非增值活动。这些看似微小的资讯,却是影响效能与质量的重要因素。
当缺乏完整且即时的制程数据,质量管理便无法建立在真实情境之上,导致异常状况难以及时发现,质量问题的可追溯性降低,最终可能影响产品一致性与整体生产稳定性。
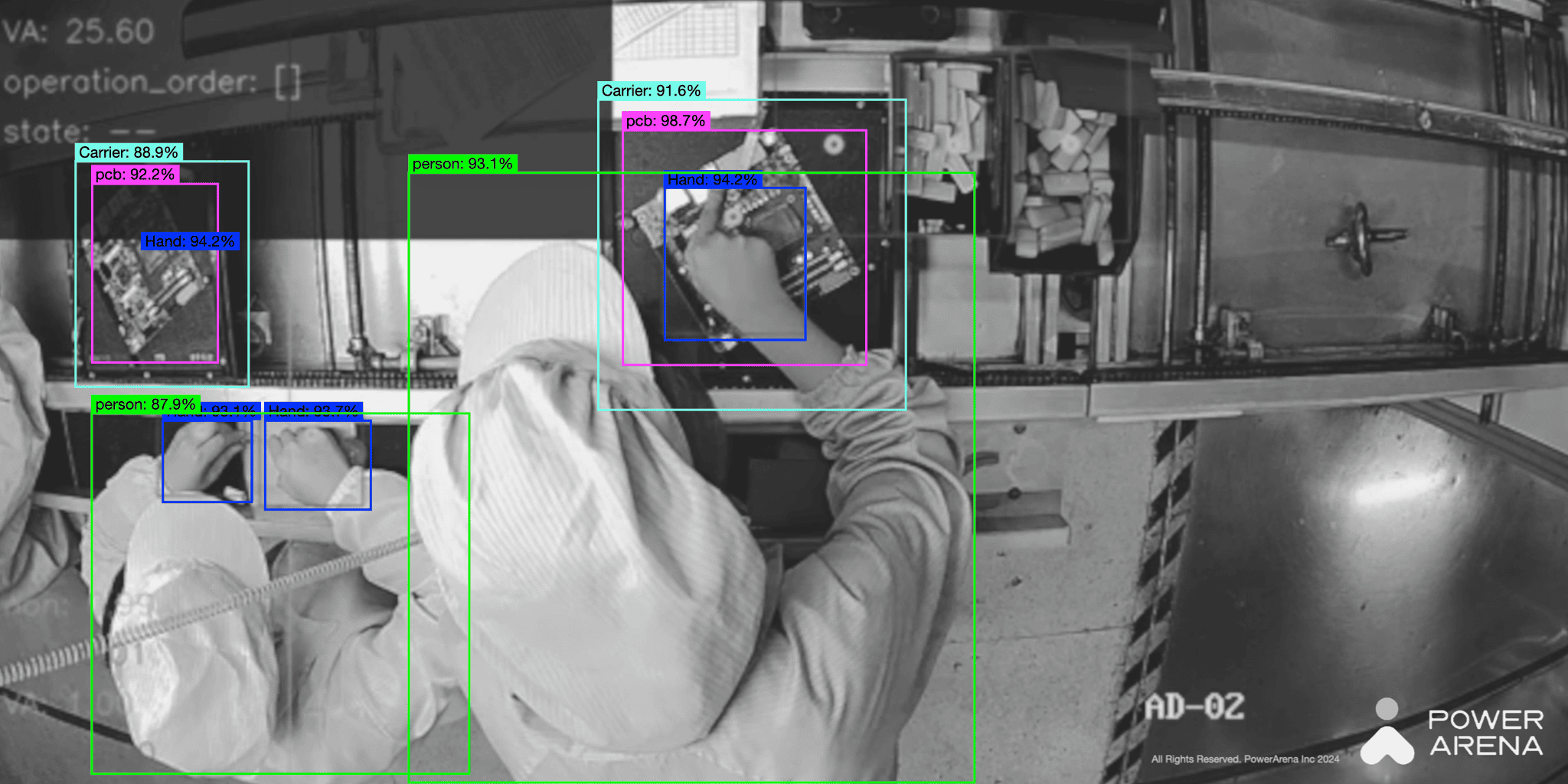
HOP 人因作业平台以 AI 视觉技术导入产线管理,自动记录与灵活分析生产数据。
HOP 人因作业平台整合多项生产管理工具的功能,透过 AI 视觉技术,实现 24 小时不间断地纪录关键生产数据,例如周期时间(Cycle Time)、闲置时间(Idle Time)等。这些数据经系统即时分析后,会自动产出可视化报告。特别是在人工参与程度高、易变动的产线中,HOP 有效解决了「数据无法即时取得」的问题,同时也帮助人员在当下即时发现效率异常,进行快速调整与质量改善。
4. 难以建构完善的生产履历
许多工厂仍停留在手动记录数据,缺乏能整合影像、数据与根因追踪的系统,导致在发生异常或客诉时,无法快速还原问题发生的完整过程。
目前,许多品牌商也已开始关注生产可追溯性与流程透明度,若代工厂无法为产品提供清晰的生产履历,可能影响品牌对其质量控管能力的信任。因此,完善的生产履历不仅是质量溯源的基础,更是建立品牌合作关系的关键条件。
5. 管理经验无法传承与追踪
受地缘政治影响,许多在中国深耕多年的制造企业,开始采取产地分散策略,以提升供应链的弹性与抗风险能力。东南亚因具备地理位置优势及相对低廉的劳动成本,迅速成为制造业迁移的首选。
然而,与中国、台湾等成熟制造基地相比,企业发现,在越南、泰国等地的新厂区,生产质量与效率普遍落后 20% 至 30%。这是因为当地面临更多不可控的生产变因,例如高员工流动率、更频繁的 SOP 违规情况,以及缺乏具备经验的本地人才,使得母厂的管理模式难以复制。
在这种情况下,企业只能仰赖来自中国或台湾管理团队进驻救火,虽然有助于短期改善,但当外部支援人员离开后,当地团队能否延续改善行动、执行成效能否被追踪,往往都成为企业在海外扩产过程中的一大痛点。
做好质量管理的成功案例
AI 视觉在生产过程中的防错防呆
整合 AGV , MES 与 AI 视觉的制程中質量管理系统
这家知名机车品牌,近年致力于智慧工厂的部属。初期已导入由 MES 和 AGV 构成的防错防呆机制。
随着产量的提升,工厂发现因为 MES 系统无法追溯人员的组装过程,未有效执行 SOP 的情况仍存在。
即便是电子化的 SOP,仍然无法确定人员是否有照做。
── 电动汽机车制造商的智慧制造系统及解决方案处长
透过导入 AI 视觉技术,工厂能建立起一套更完整的防错防呆机制。传统的 MES 系统对于『人员是否确实完成每一道作业动作』这一环,仍存在管理上的空白。
而 AI 视觉正好补足了这个缺口。
当作业员完成一个步骤后,只有在 AI 视觉与 MES 系统都确认动作无误,AGV 才会被允许放行;若有异常,系统会主动发出警报,并即时通知管理层。主管可以透过平板、简讯等多种渠道接收到异常通知,并利用影像回放快速确认现场状况,做出是否放行的判断。这不仅提高了品质控管的即时性,也降低了人为错误对生产质量的影响,让 SOP 真正落实在每一道工序之中。
LLM 自动化生产管理与质量管理工作
过去,生管人员必须透过 SQL 等资料库语法查询产线数据,不仅耗时繁琐,一旦语句错误或资料表结构设计不良,更可能导致错误判读与决策偏差。同时,系统内的资料常常不够完整或即时,即使耗费时间分析,也未必能真实反映当下的产线状况。
为了解决这些痛点,仁宝电脑开发了基于 LLM 的产线管理系统,并结合 PowerArena 的 AI 视觉技术,透过实际产线上搜集的即时数据训练模型。这使管理者能以自然语言查询产线资讯,即可快速取得精确、即时的生产与品质数据,不仅提升了生管与品管的效率,也强化了跨部门决策力。
结论
1. 整合生产现场资讯
在传统的电子工厂的内,由于部门间使用的管理方法、纪录数据的时间不同,导致改善会议难以聚焦。
在与管理层回顾生产状况的时候,各部门的观点及解决方案都不太一样,如果系统可以给我客观资料,我可以很快对症下药。
—— 电子大厂越籍工业工程师
HOP 人因作业平台是整合性的生产管理、质量管理系统,协助管理层运用统一的追踪系统,看见当前生产异常以及关键肇因,协助管理层做出更加准确的决策。
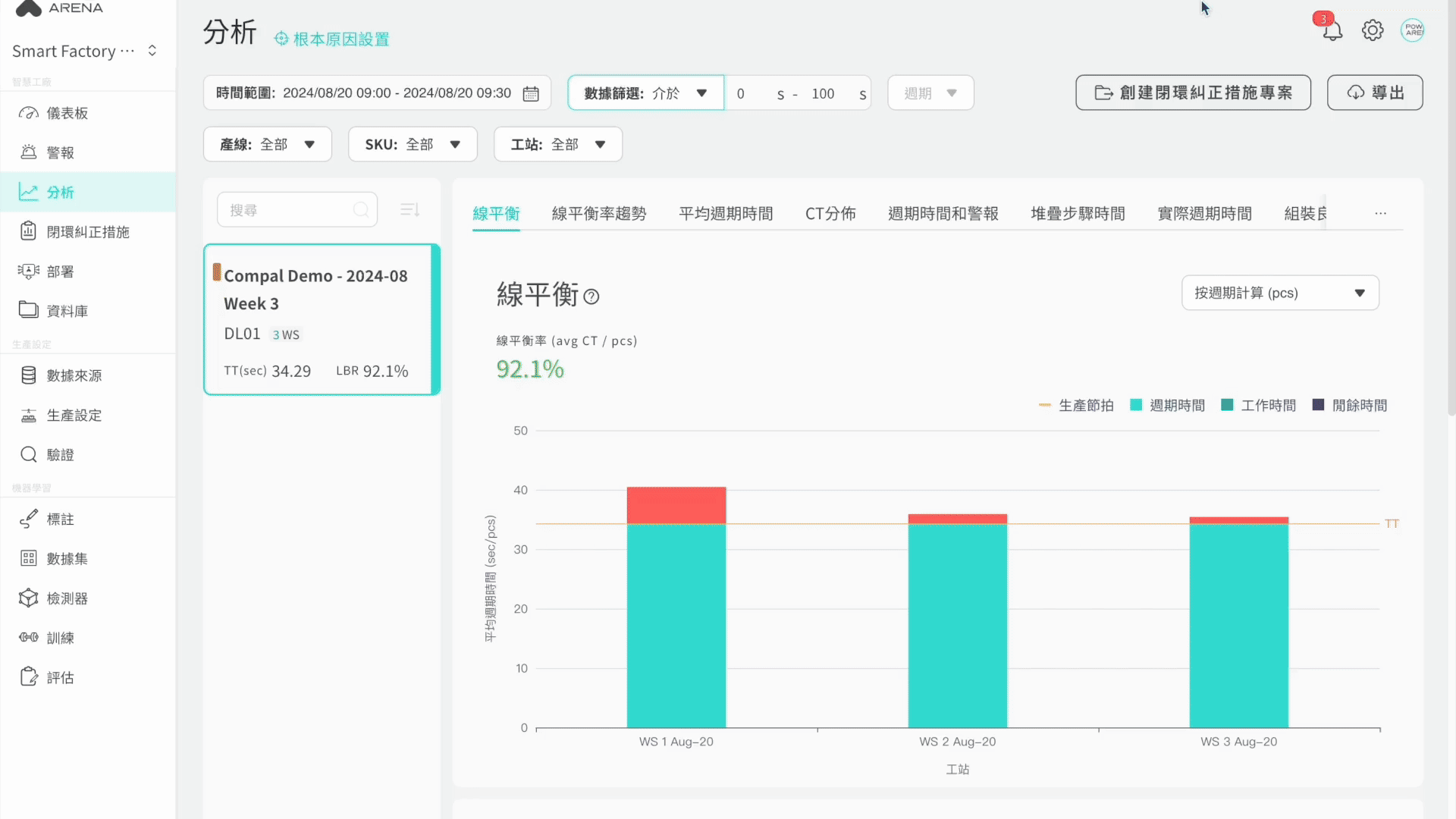
HOP 人因作业平台以生产影像+ AI 视觉分析报告,提供完整、可视化与即时的生产情况解析。
2. 以『数据』驱动改善措施
传统的品质管理仰赖人工纪录与分析,难以全面掌握产线上的各项细节。随着产线规模与复杂度不断增加,单靠人力已难以有效支援持续改善的需求。
以人工检视产线,每项产品需耗费高达 48 小时进行时间研究。
AI 视觉技术可自动化搜集与分析产线数据,大幅减轻人力负担,让品质管理人员能将重心转向策略性决策与优化规划。
同时,HOP 人因作业平台搭配产线历史影像纪录,让决策者能回溯并精准定位问题发生的环节。品质管理人员可根据 AI 标记的问题影像,准确识别瓶颈,并以数据为依据提出针对性改善。
3. 数位化追踪改善成效
传统品质管理缺乏具体数据佐证,导致改善成效难以验证,影响持续改善的进度与管理信心。
HOP 人因作业平台提供数位化纪录功能,让每项改善措施都有清晰的历程与依据。这不仅方便现任管理人员追踪成果,也为后续接手者建立可追溯、可复用的知识资产,显著降低沟通成本,加快问题解决流程。
透过持续的数据追踪与成效分析,企业能验证改善是否真正落地,并持续优化产线表现,实现真正可持续的品质改善。
Table of Contents