By Sursha Wu
品質管理是什麼?
品質管理(Quality Management),又稱品管,是企業確保產品或服務能持續符合顧客需求與法規標準所進行的核心活動。無論是哪種行業,『做好品質管理』始終是提升顧客信任、降低營運風險,以及推動企業穩健成長的關鍵。
以製造業為例,品質管理通常著重於產品規格的一致性與生產流程的穩定性。
隨著生產日益複雜、跨廠甚至跨國協作成為常態,製造商逐漸意識到,唯有導入更進階的品質管理系統,才能提升管理效率、降低人力成本,減少對現場經驗的高度依賴,並實現更即時、主動的品質管理。
品質管理的 3 個重點
1. 完善製程品管,預防勝於檢驗
在製造業中,製程內品質管制(IPQC)扮演關鍵角色,其核心精神是『及早發現、立即修正』。比起事後檢驗,更重要的是在問題還小、還能控制的階段就將它解決,避免錯誤擴散到最終成品。
只要在產線上能發現問題,馬上檢修,甚至都不需要費用。可是一旦這個東西放到市場上面,費用都很嚇人。
── 電動汽機車製造商的智慧製造系統及解決方案處長
案例解析:德國豪華汽車品牌的召回風暴
德國某知名豪華汽車品牌於 2022 年內部就曾偵測到煞車系統異常。瑕疵原因來自供應商的人工組裝作業未確實清潔電路板,進一步損害煞車系統,影響車輛安全。
此外,因未能及時在製程端發現錯誤,導致同樣的異常生產存在產線長達 2 年,最終累積超過 150 萬輛車輛被召回,維修與處理成本預估高達 10 億歐元。嚴重的是,最終管理層仍無法肯定問題車輛皆已被回收,導致顧客與經銷商信心大幅下降,媒體與市場也紛紛質疑該企業的品質控管與供應鏈監督能力,導致公司股價重挫近 28%。
—— News reference: 彭博社(Bloomberg)Sep. 16. 2024
這起事件凸顯了製程品管與生產履歷建立的關鍵性:
- 製程控管失效的代價高昂
- 高安全性產業風險更高
- 製程防錯防呆是關鍵
- 建立生產履歷有助於問責與溯源
如何用 AI 視覺做到製程防錯防呆?
2. 透過品管方法論,持續改善作業流程
3. TQM 全面品質管理,建立全員品質文化
品質管理的 5 種工具
透過有邏輯、有步驟的方法工具,企業可以更有效率地找出問題根源、建立可追蹤的改善機制,最終實現整體品質與良率的上升。
1. PDCA 循環
PDCA 循環(PDCA Cycle),即計劃(Plan)、執行(Do)、檢查(Check)、行動(Act)。最早由美國著名管理學家愛德華茲·戴明(Edwards Deming)於 20 世紀提出的系統化品質管理概念。
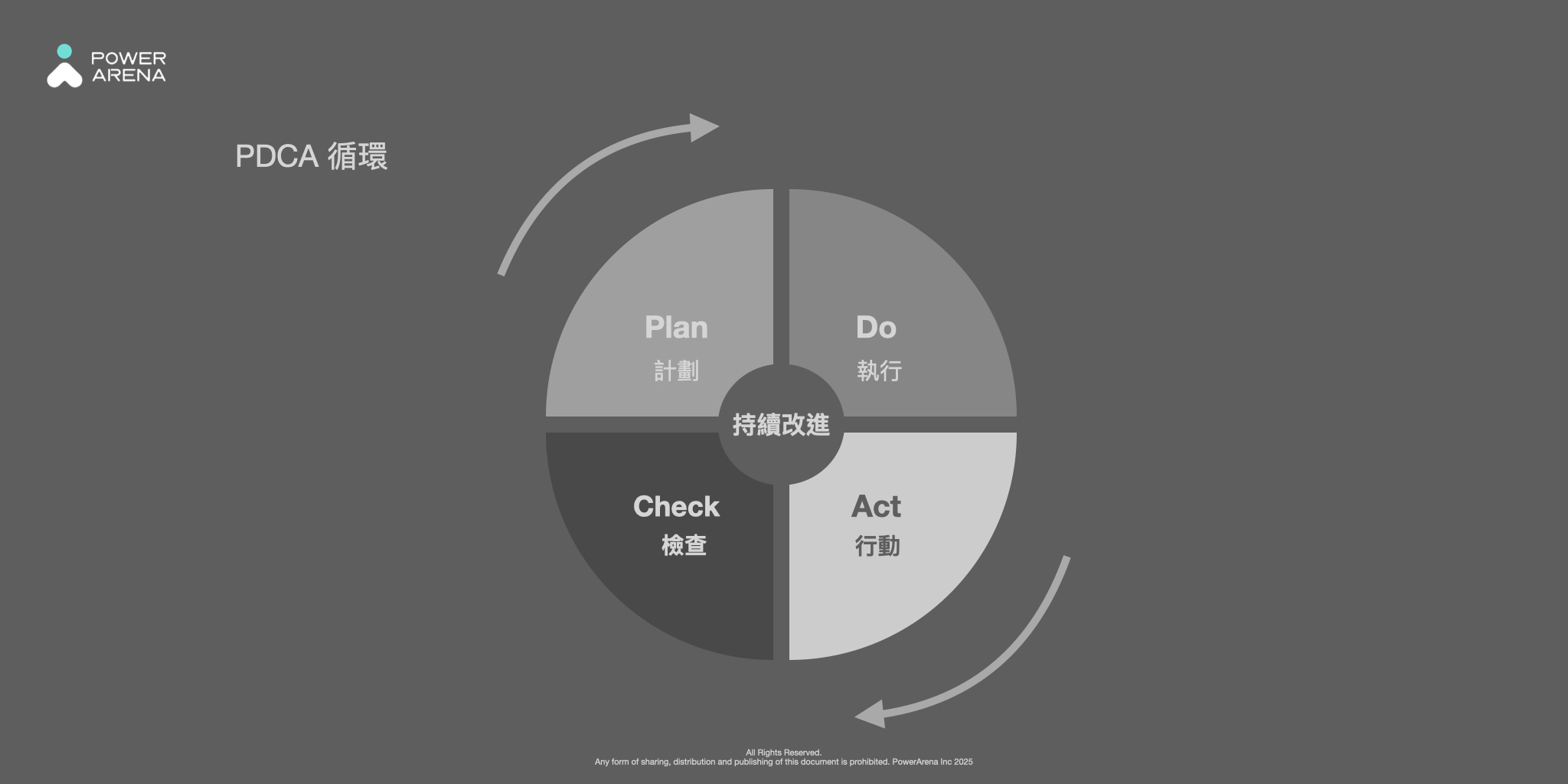
透過 PDCA 循環方法,持續改進作業流程,提升品質。
完成一次流程之後,以前次結果為基礎,再建立下一個目標進行循環。直至達成品質管理目標。
2. FMEA 失效模式與效應分析
FMEA(Failure Mode and Effects Analysis)是一種系統化的預防性工具,廣泛應用於產品設計與製造流程中,目的是在工廠投入大量生產前,提前辨識潛在失效模式,並評估其對產品與系統的影響,進而訂出處理優先順序與改善對策,避免不良品流入市場、造成召回、售後維修與品牌損害等高昂代價。
3. CLCA 閉循環修正措施
CLCA (Close Loop Corrective Action)是一套強調『發現問題、追查根因、執行改善並驗證是否有效』的閉環品質管理流程,最早由 DELL 公司導入並廣泛應用於製造業。它的核心目的在於防止問題再次發生,確保每次異常都能真正被解決、留下可複用的改善經驗。
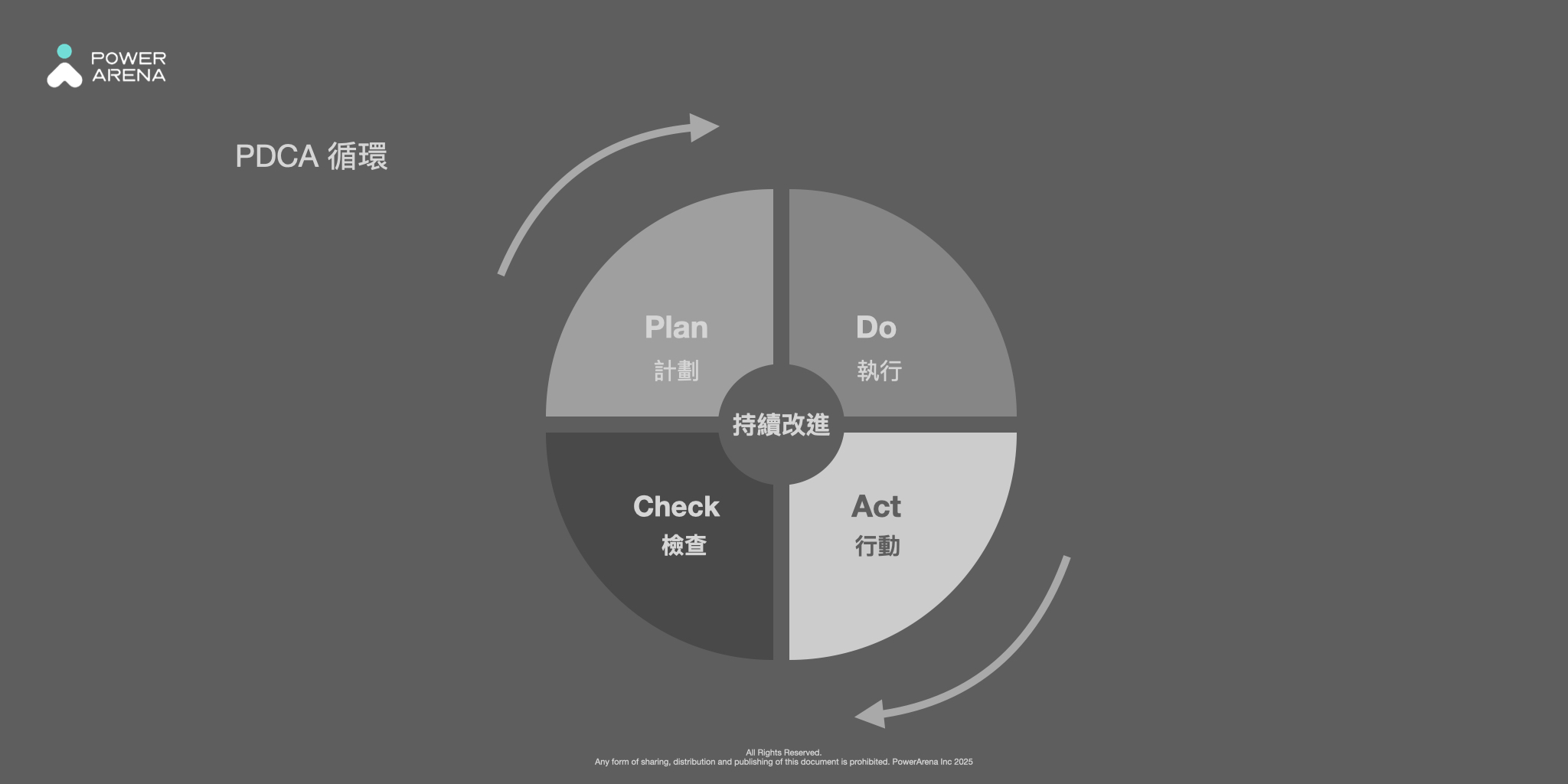
CLCA (Close Loop Corrective Action) 閉循環修正措施流程。
工廠例子是…

工廠利用 HOP 人因作業平台中的 CLCA 功能,完整保留產線改善紀錄。
4. 六標準差 Six Sigma
5. 品質管理系統(如 ISO 9001)
品質管理的各職務分類與內容
以下是製造業中常見的品質管理職務分類及其工作內容:
- 品質保證(QA, Quality Assurance)
- 品質管制(QC, Quality Control)
- 製程品質工程師(QE, In-Process Quality Engineer)
- 供應商品質管理(SQE, Supplier Quality Engineer)
- 品質數據與系統管理(QMS / Data Analyst)
隨著智慧工廠與製造數位化的發展,大型企業開始出現更專職的「品質數據分析師」與「系統管理人員」角色。他們主要負責企業內部的品質管理系統(QMS)維運,並整合來自現場的各類檢驗數據,進行分析與視覺化呈現,讓管理層能以數據為依據進行決策。
具備技術背景的分析師,可能進一步參與 AI 模型的開發與導入,用於建立品質預測模型、異常預警系統等應用。
製造業在面臨品質管理的 5 個問題
1. 生產 SOP 執行不足
許多產線雖已建立了生產 SOP,但這些規範往往未能充分考慮現場實際操作的習慣、環境限制,或是流程中可能出現的變異情境。導致 SOP 雖存在,卻難以在實務中完全落實,可能直接影響產品品質。
此外,即使工廠已導入生產管理系統,雖然能有效蒐集設備層級的數據,卻普遍難以即時掌握人工作業流程中的異常狀況。

HOP 人因作業平台,能夠自動搜集與分析生產數據的系統,並能以 AI 視覺建立防錯防呆機制。
2. 難以在製程當下排除瑕疵
在許多工廠中,製程瑕疵若未能在當下即時被發現,往往會因為下一站料件的覆蓋或裝配而被掩蓋,難以在品檢端檢出,而是在市場端客訴時才曝光。
另一方面,許多工廠現今也面臨高離職率的問題,新進員工對操作流程不熟悉,極易產生品質偏差。對於第一線的管理者來說,即使再強化教育訓練,也難以持續監控每位員工的操作細節。
當老手與新手混在線上作業時,生產效率、生產品質常受到影響。僅依賴最終品檢(Final Quality Control)篩出不良品,必會增加返工成本與材料浪費,提高整體生產成本。
HOP 人因作業平台透過 AI 視覺技術,協助現場人員即時追蹤作業員的操作行為,確保每個步驟皆符合 SOP。系統於產線部署攝影機,不僅記錄整個生產過程,更能在製程發生的當下即時判斷作業是否偏離標準,主動識別異常。

HOP 人因作業平台以 AI 視覺技術追蹤人員動作,並及時回報 SOP 違反情況。
有自動化製程防錯防呆需求?
3. 無法全面生產資訊搜集與分析
在傳統管理模式下,工業工程師必須投入大量時間進行人工觀察與記錄,但這樣的方式無法覆蓋所有時段,也難以精確掌握像是作業員離崗、操作空檔等非增值活動。這些看似微小的資訊,卻是影響效率與品質的重要因素。
當缺乏完整且即時的製程數據,品質管理便無法建立在真實情境之上,導致異常狀況難以及時發現,品質問題的可追溯性降低,最終可能影響產品一致性與整體生產穩定性。
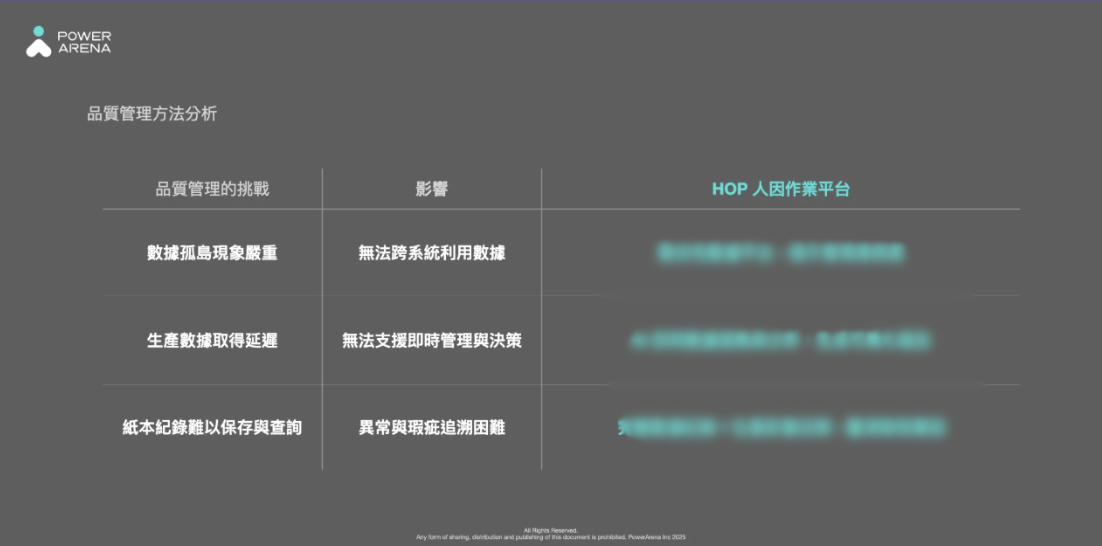
HOP 人因作業平台
HOP 是什麼?優勢與應用一次看
4. 難以建構完善的生產履歷
許多工廠仍停留在手動記錄數據,缺乏能整合影像、數據與根因追蹤的系統,導致在發生異常或客訴時,無法快速還原問題發生的完整過程。
目前,許多品牌商也已開始關注生產可追溯性與流程透明度,若代工廠無法為產品提供清晰的生產履歷,可能影響品牌對其品質控管能力的信任。因此,完善的生產履歷不僅是品質溯源的基礎,更是建立品牌合作關係的關鍵條件。
5. 管理經驗無法傳承與追蹤
受地緣政治影響,許多在中國深耕多年的製造企業,開始採取產地分散策略,以提升供應鏈的彈性與抗風險能力。東南亞因具備地理位置優勢及相對低廉的勞動成本,迅速成為製造業遷移的首選。
然而,與中國、台灣等成熟製造基地相比,企業發現,在越南、泰國等地的新廠區,生產品質與效率普遍落後 20% 至 30%…
做好品質管理的成功案例
AI 視覺在生產過程中的防錯防呆
整合 AGV , MES 與 AI 視覺的製程品管系統
這家知名機車品牌,近年致力於智慧工廠的部屬。初期已導入由 MES 和 AGV 構成的防錯防呆機制。
隨著產量的提升,工廠發現因為 MES 系統無法追溯人員的組裝過程,未有效執行 SOP 的情況仍存在。
即便是電子化的 SOP,仍然無法確定人員是否有照做。
── 電動汽機車製造商的智慧製造系統及解決方案處長
LLM 自動化生管品管工作
過去,生管人員必須透過 SQL 等資料庫語法查詢產線數據,不僅耗時繁瑣,一旦語句錯誤或資料表結構設計不良,更可能導致錯誤判讀與決策偏差。同時,系統內的資料常常不夠完整或即時,即使耗費時間分析,也未必能真實反映當下的產線狀況…
結論
1. 整合生產現場資訊
在傳統的電子工廠的內,由於部門間使用的管理方法、紀錄數據的時間不同,導致改善會議難以聚焦。
在與管理層回顧生產狀況的時候,各部門的觀點及解決方案都不太一樣,如果系統可以給我客觀資料,我可以很快對症下藥。
—— 電子大廠越籍工業工程師
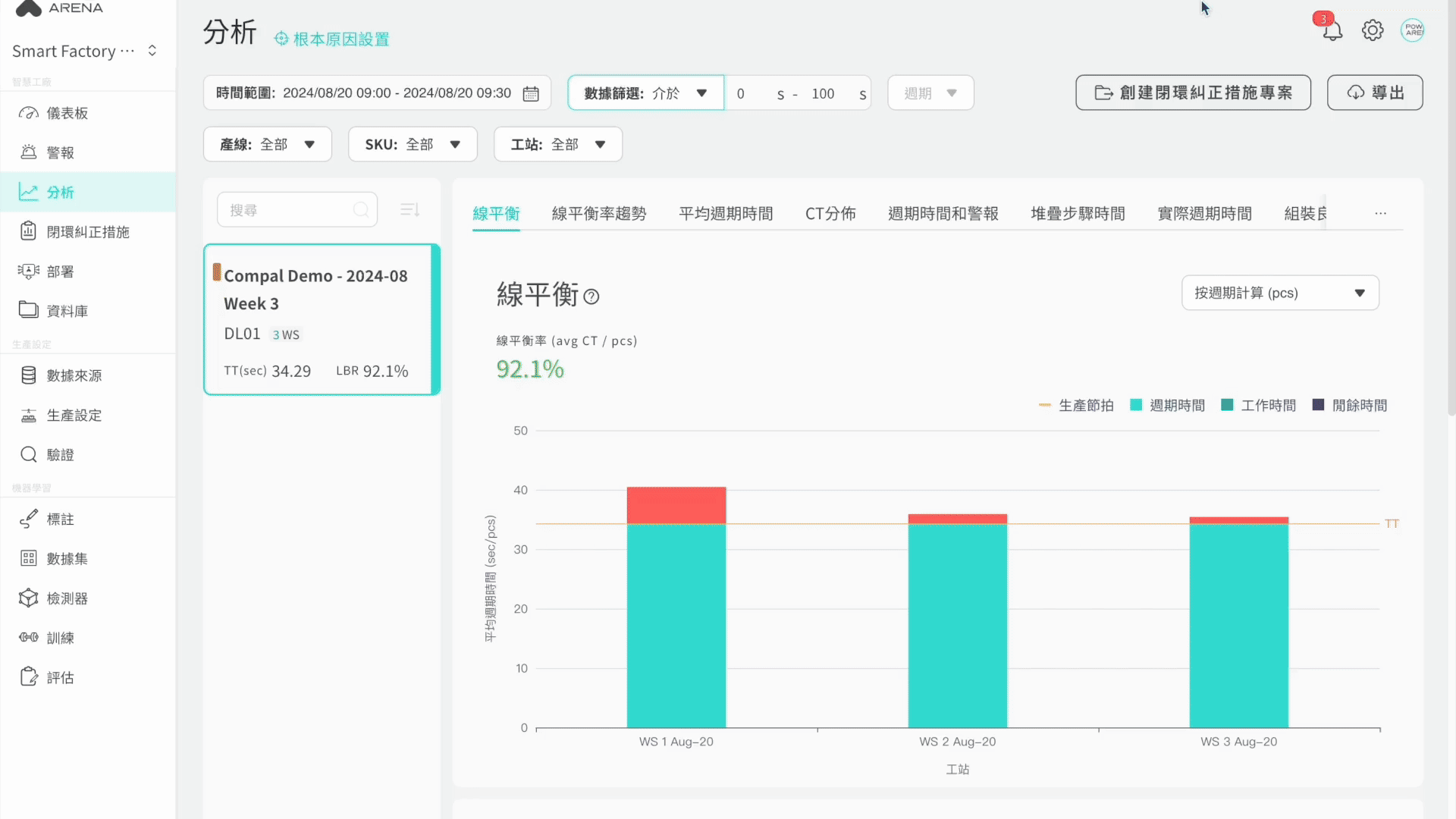
HOP 人因作業平台以生產影像+ AI 視覺分析報告,提供完整、可視化與即時的生產情況解析。
想了解更多 AI 製程品管?
2. 以『數據』驅動改善措施
傳統的品質管理仰賴人工紀錄與分析,難以全面掌握產線上的各項細節。隨著產線規模與複雜度不斷增加,單靠人力已難以有效支援持續改善的需求。
以人工檢視產線,每項產品需耗費高達 48 小時進行時間研究。
AI 視覺技術可自動化蒐集與分析產線數據,大幅減輕人力負擔,讓品質管理人員能將重心轉向策略性決策與優化規劃。
3. 數位化追蹤改善成效
傳統品質管理缺乏具體數據佐證,導致改善成效難以驗證,影響持續改善的進度與管理信心。
HOP 人因作業平台提供數位化紀錄功能,讓每項改善措施都有清晰的歷程與依據。這不僅方便現任管理人員追蹤成果,也為後續接手者建立可追溯、可複用的知識資產,顯著降低溝通成本,加快問題解決流程。
透過持續的數據追蹤與成效分析,企業能驗證改善是否真正落地,並持續優化產線表現,實現真正可持續的品質改善。
Table of Contents