By Sursha
2025 年 6 月,全球知名充电宝品牌 Anker 安克创新,因部分产品存在过热与爆炸风险,在全球多个市场启动大规模召回行动。
美国消费品安全委员会(Consumer Product Safety Commission, CPSC)于 6 月 12 日发布紧急公告,宣布召回逾 115 万颗充电宝,并指出已接获 19 件起火与爆炸事故通报,包含烧伤与财产损失,累计损失金额超过 6 万美元,同时呼吁消费者立即停止使用相关产品。
中国市场召回超过 71 万颗产品,且相关电芯与制程问题仍在调查中;日本方面,召回数量达数十万颗,是日本市场最大规模的一次充电宝召回事件。
这起事件在短时间内波及多个主要市场,对 Anker 品牌声誉造成巨大冲击,也再次凸显电子产品制造行业必须强化的关键课题:从制程品控到追溯机制,将成为应对安全风险与信任挑战的重要防线。
法规制度的回应:微小瑕疵造成的飞安风险
Anker 的召回事件并非个案。近期,中国制造充电宝品牌罗马仕 ROMOSS 也因安全隐患召回逾 50 万颗产品。更早前,韩国釜山航空亦曾传出疑似充电宝自燃,导致机舱起火,凸显充电宝对航空安全构成的潜在风险。
据中央社报道,今年 6 月 13 日,一班自郑州起飞的上海航空航班上,一名旅客的充电宝突然冒烟,所幸机组人员与旅客及时处理,最终安全降落。
为应对相关风险,中国民航局近日发布紧急通知,明确禁止携带未经 3C 认证或已列入召回名单的充电宝登机。虽并非针对单一品牌,却反映出监管机构正在加强对高风险电子产品的管控。
但这也引发一个更根本的问题:拥有认证标志是否就代表真正的安全?
事件回顾:品牌商该如何完善供应商的尽职调查?
根据 Anker 安克创新于官网发布的说明,此次事件起因于供应商使用了未经品牌方授权变更的原材料。该批次电芯在长期循环使用下,可能出现隔膜绝缘失效,进而导致过热甚至起火风险。
这反映出品牌方对供应商制程掌控不足,在原材料变更、制程细节与最终质量之间,缺乏足够的透明度与实时联动。尤其在物料与制程环节未建立『绑定与审批机制』,一旦供应商私自调整用料或流程,品牌方将难以及时察觉与介入。
是否『看得见』、『管得好』每一个生产步骤?
对于多数电子代工厂而言,生产规模庞大、产线复杂,各工位所执行的操作流程多且细,作业人员发生操作错误在所难免。而对于现场管理者来说,也难以及时掌握每一个工位的操作细节,错料、漏步、作业顺序错误等问题往往只能事后追查。
这种挑战对代工厂而言已不小,对于品牌方更是难上加难。当品牌方缺乏一套可实时查看、可信赖且自动化的质量管理系统时,对外部供应链的制程与质量就难以深度掌控。
一旦出现瑕疵或异常,往往难以及时定位问题并进行风险管控。
解决方案:制程影像与 AI 视觉的实质助力
1. 实时管理:AI 视觉提升制程即时管理能力
PowerArena 的 HOP 人因作业平台结合 AI 视觉技术,具备实时识别与分析能力,能全天候管理现场作业,判断来料是否正确、操作是否依照 SOP、制程时间是否异常等。
当出现组装角度偏差、料件使用错误、步骤遗漏或工时过长等异常情况时,系统会即时发出警报,通知管理人员介入处理,协助现场迅速排查问题,防止不良品流入下一道工序。
在换线频繁的生产环境中,HOP 可自动切换对应的 AI 模型,精准适配不同产品的料件与操作标准,确保生产过程持续稳定且一致。
通过这种「即时响应、即时修正」的机制,企业得以将质量管理从事后补救,推进为更主动、可控的制程管理与防错机制。
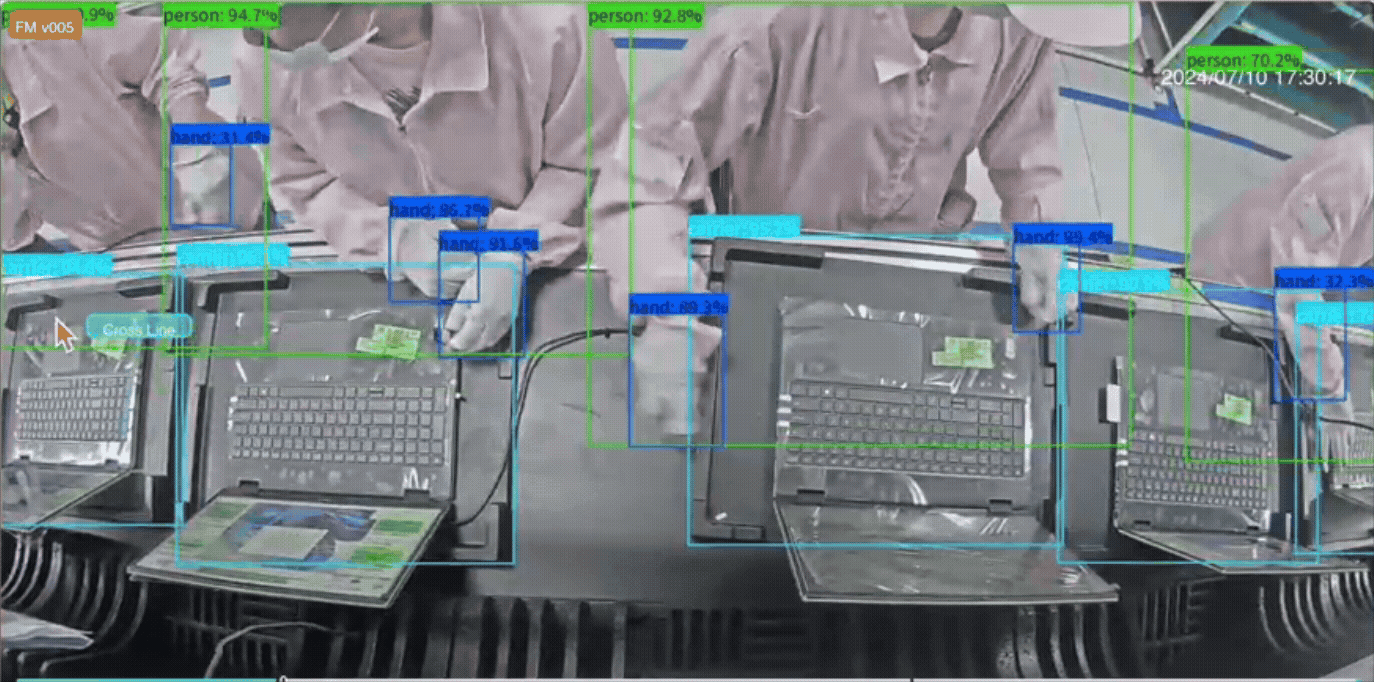
如离开工位或超过标准作业时间等情况,系统会自动标记并通报线长。视频来自 Compal 示范产线。
2. 制程影像记录:为每一项产品建立完善『生产履历』
相较于传统仅留下工单、报表或手写备注,这些记录不仅可能遗漏关键信息,也难以全面反映现场情况。『生产影像资料』则能如实呈现每一道工序与操作细节,是更可靠、可验证的质量依据。
PowerArena 的 HOP 人因作业平台可为每一件产品建立完整的『生产履历』,将制程影像、作业时间、工位信息与使用料件等关键信息串联整合。
当日后需要追查问题原因时,无需逐条翻阅资料或依赖现场人员反馈,管理者可直接调出对应时间、工位与影像画面,迅速厘清问题原因,提升应变效率与准确性。
此外,系统支持跨部门、跨厂区甚至跨国查阅,让各单位都能实时掌握一致的生产信息,大幅提升管理透明度与沟通效率。
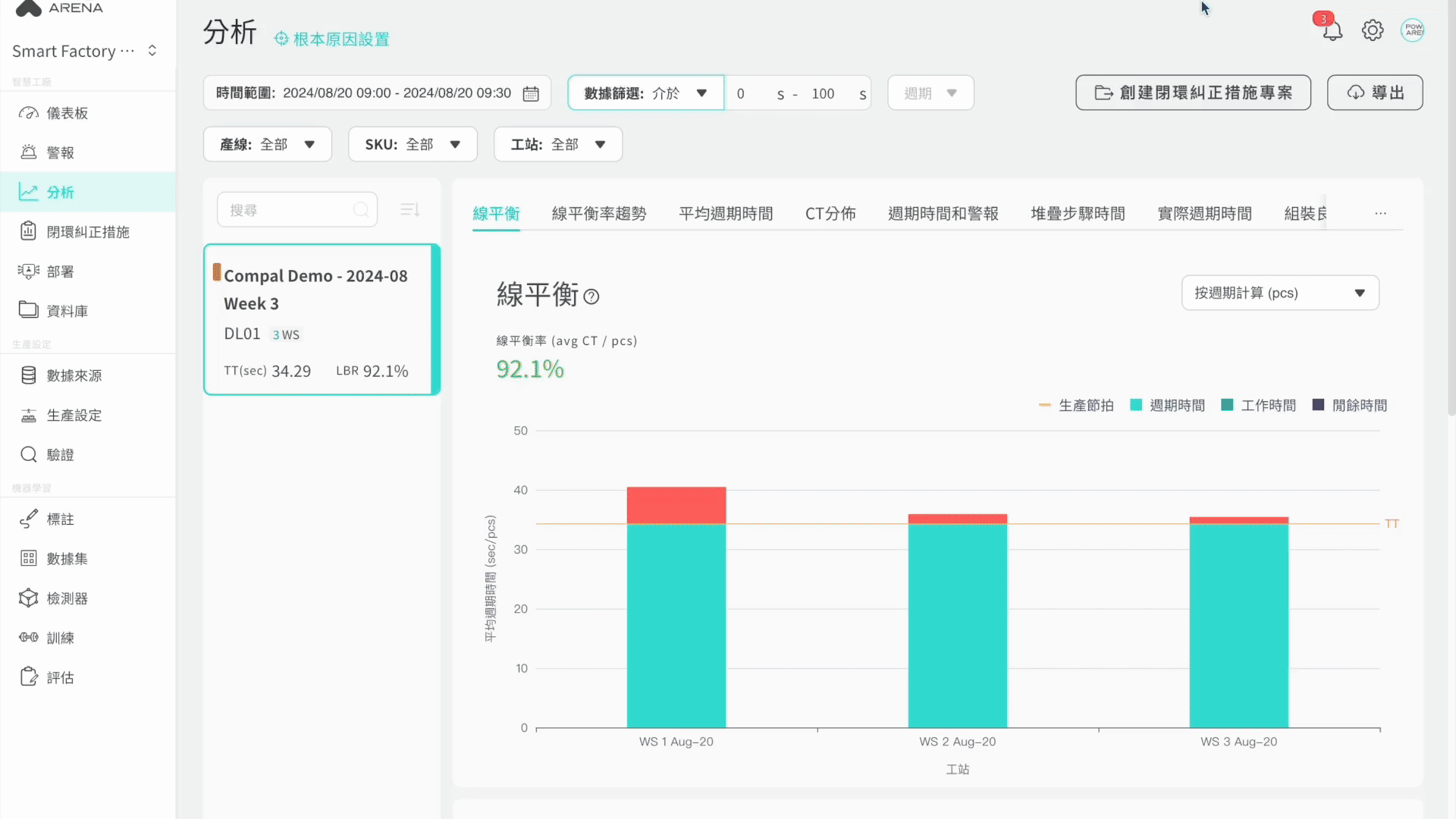
如离开工位或超过标准作业时间等情况,系统会自动标记并通报线长。视频来自 Compal 示范产线。
了解更多:关于制程的影像追踪与自动化撷取
3. 精准追溯:召回范围可控,风险管理有据可依
当产品发生异常、引发召回或安全争议时,企业能否迅速厘清问题根源,往往决定后续处理的效率与品牌信任的恢复速度。
实际情况中,多数企业在面对产品风险时,常因无法定位问题来源,只能选择「全面召回」。其主因往往是产品与实际生产工位或产线间缺乏绑定与数据对应,导致追溯困难。更严重的是,若无法确定瑕疵从哪一条产线、哪个时间点开始出现,瑕疵品可能持续流入市场,进一步扩大风险与品牌损失。
PowerArena 的 HOP 人因作业平台可在生产过程中自动将产品与工位资料绑定,当异常发生时,管理者能以产品批次、生产工位、生产时间任一信息回调生产影像,获得「影像 + 数据」的双重佐证,有效锁定影响范围,确保召回落实并控制风险扩散。
结语:制程品控,是风险控制的起点,也是品牌韧性的基础
对供应商而言,通过更自动化、数字化的系统强化制程品控,能在生产当下即排除瑕疵,并为每件产品建立完整的生产履历,不仅有效降低返工与赔偿风险,也有助于建立品牌客户的信任与确保合规。
对品牌商而言,拥有一套可追溯、可信赖、可获取的制程管理系统已成为基本配置,不仅提升对供应端的掌控力,更能实现生产过程的透明化,为品质把控提供更强有力的支撑。
在供应链日益复杂、质量与安全标准不断提升的当下,从源头落实制程透明与质量记录,不仅是降低风险的手段,更是企业打造韧性、提升竞争力的关键所在。
想为您的电子产品产线建立可靠的生产履历吗?欢迎提出您的需求,由专人提供报价。
Table of Contents