By Sursha
In June 2025, Anker, a global leader in portable chargers, launched a large-scale recall after some products were found to overheat and catch fire.
The U.S. Consumer Product Safety Commission announced on June 12 that more than 1.15 million units were affected. There were 19 reports of fires and explosions, including injuries and property damage totaling over 60,000 U.S. dollars. Consumers were urged to stop using the product immediately.
In China, more than 710,000 units were recalled. Japan also issued a recall involving hundreds of thousands of units, marking the country’s largest-ever portable charger recall. The incident quickly spread across major markets and damaged Anker’s brand reputation.
This case shows how crucial process quality control and production traceability are in addressing safety risks and maintaining customer trust.
Regulatory Response: Minor Defects Can Create Major Safety Hazards
Anker is not alone. Another Chinese brand, ROMOSS, recently recalled over 500,000 units for similar safety concerns. Earlier, a portable charger reportedly caught fire on a Busan Air flight in South Korea.
According to media reports, on June 13, a power bank began emitting smoke on a Shanghai Airlines flight departing from Zhengzhou. The situation was handled quickly, and the plane landed safely.
To reduce such risks, the Civil Aviation Administration of China issued a notice banning passengers from bringing power banks that lack 3C certification or are on recall lists.
This raises an important question:
Does having a certification truly mean the product is safe?
Behind the Incident: Supplier Audits and Process Transparency
Anker’s official statement revealed that the issue came from a supplier who used unauthorized materials. The batteries from that batch were more likely to fail after repeated use, increasing the risk of overheating.
This shows a lack of visibility and control over supplier processes. When brands do not have approval and monitoring mechanisms in place, it becomes difficult to detect unauthorized changes in materials or production steps.
In most electronics factories, the scale and complexity of production make it hard to oversee every detail. Mistakes like using the wrong part or skipping a step are common. Managers on the ground cannot monitor every workstation at every moment, making quality issues harder to catch before they escalate.
For brand owners, the challenge is even greater. Without a real-time and automated quality management system, it is difficult to gain insight into what suppliers are doing on the production floor.
Solutions: How AI Vision and Production Video Improve Control
1. Real-time Process Oversight
PowerArena’s HOP (Human Operation Platform) uses AI vision to monitor tasks continuously. It can detect if materials are correct, if workers follow standard procedures, and if task durations deviate from expected norms.
When problems such as misalignment, wrong parts, skipped steps, or extended work time occur, the system sends alerts immediately. This helps frontline teams respond quickly and avoid sending faulty products to the next stage.
In fast-paced production environments with frequent product changes, HOP automatically switches AI models to match different parts and procedures, ensuring consistency across tasks.
This shift from reactive to proactive quality control helps reduce errors and keeps processes stable.
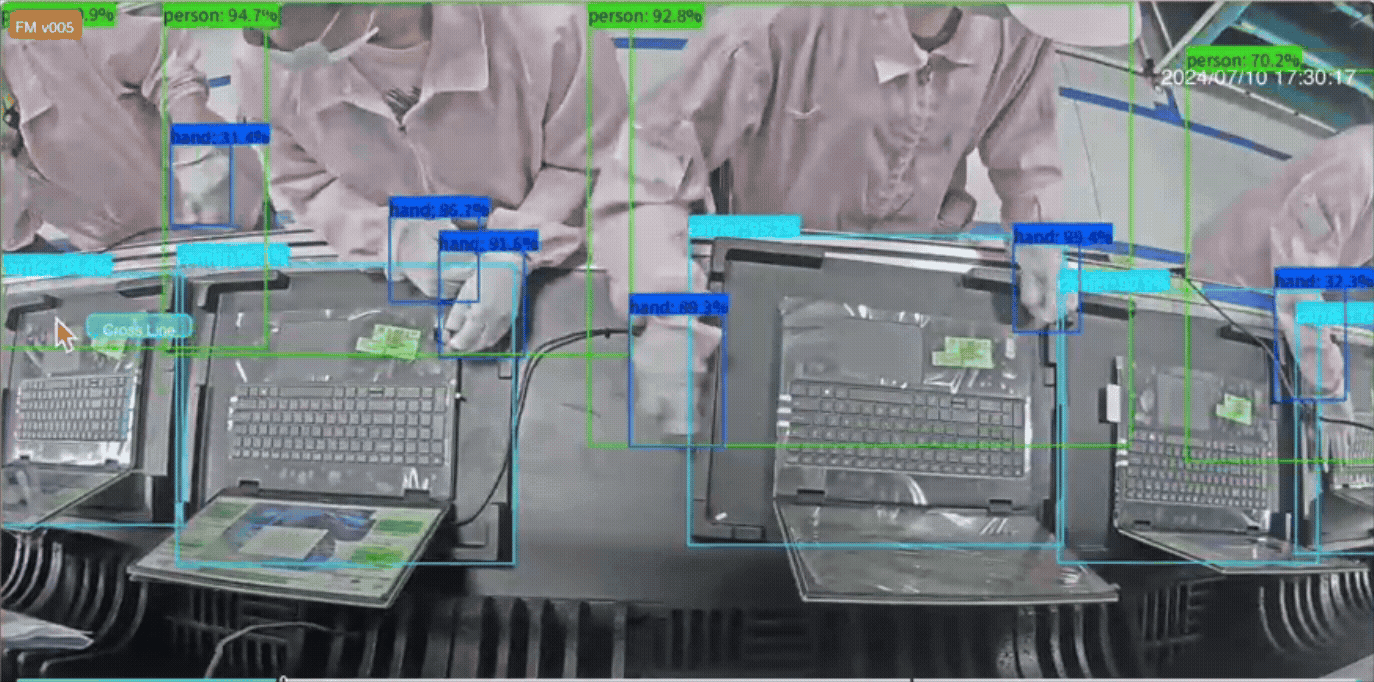
Situations such as leaving the workstation or exceeding standard operation time are automatically flagged by the system and reported to the line supervisor. Video footage: Compal’s POC demonstration line.
2. Complete Production Records with Video Data
Traditional records, such as manual data collection and reports, often miss critical information and cannot fully reflect what happened at the workstation.
HOP automatically builds a full production history for each unit, including video footage, task duration, station details, and part information.
If an issue arises later, managers can instantly retrieve specific time stamps, stations, and visual evidence, reducing time spent on investigations and improving response accuracy.
The system also supports access across departments, factories, and regions, helping teams work with consistent and transparent data.
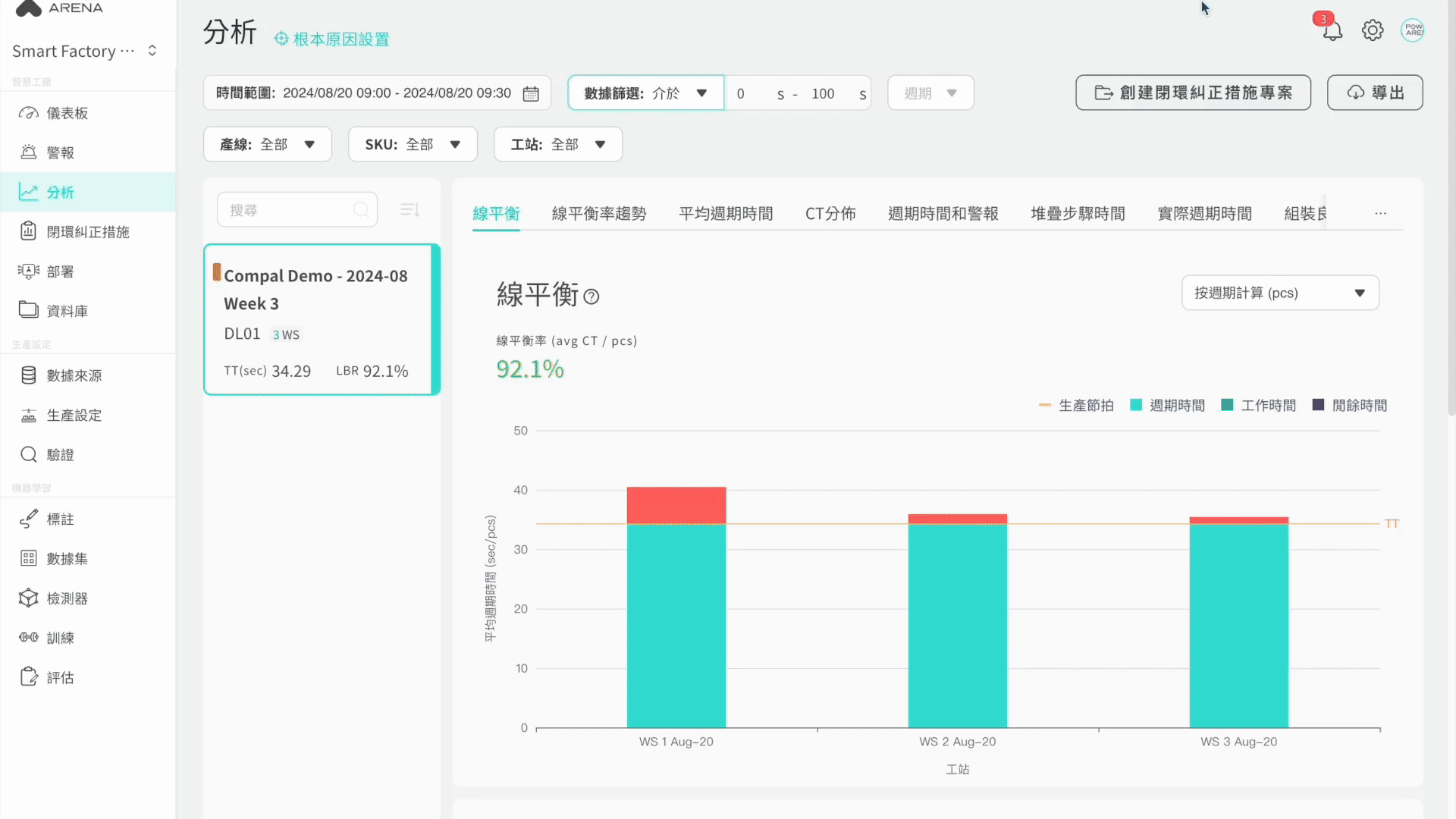
PowerArena’s HOP uses production video recording and analysis to help managers automatically identify and locate root causes. Video footage: Compal’s POC demonstration line.
Explore Video Tracking & Capture in Manufacturing
3. Accurate Traceability for Safer Recalls
When a safety incident occurs, the ability to quickly identify the root cause determines how efficiently the issue can be contained.
In many companies, unclear links between products and specific production lines make tracing difficult. This often leads to full recalls, even when only a small batch is affected.
With HOP, every product is automatically linked to its workstation data. If a problem occurs, managers can trace it using the product number, workstation, or time, and access both visual and data records to clearly define the scope of the issue.
This minimizes unnecessary recalls and prevents faulty products from reaching customers.
Conclusion: Process Quality Is the First Line of Risk Control
For suppliers, using digital systems like HOP enhances process visibility and helps eliminate defects in real time. It also builds a detailed production history for each item, reducing risks and earning customer trust.
For brand owners, a traceable, reliable, and accessible quality management system is no longer optional. It strengthens control over the supply chain and supports transparent, data-driven quality assurance.
As global supply chains become more complex and safety standards rise, ensuring production transparency from the source is not just about reducing risk. It is the foundation for building a resilient and competitive brand.
Want traceability for your electronics line? Contact us for a quote.
Table of Contents