By Sursha
2025 年 6 月,全球知名行動電源品牌 Anker 安克創新,因部分產品存在過熱與爆炸風險,在全球多個市場啟動大規模召回行動。
美國消費品安全委員會(Consumer Product Safety Commission, CPSC)於 6 月 12 日發布緊急公告,宣布召回逾 115 萬顆行動電源,並指出已接獲 19 起起火與爆炸事故通報,包含燒傷與財產損失,累計損失金額超過 6 萬美元,同時呼籲消費者立即停用相關產品。
中國市場召回超過 71 萬顆產品,且相關電芯與製程問題仍在調查中;日本方面,召回數量達數十萬顆,是日本市場最大規模的一次行動電源召回事件。
這起事件在短時間內波及多個主要市場,對 Anker 品牌聲譽造成龐大衝擊,也再次凸顯電子產品製造業必須強化的關鍵課題:從製程品管到追溯機制,將成為面對安全風險與信任挑戰的重要防線。
法規制度的回應:微小瑕疵造成的飛安風險
Anker 的召回事件並非個案。近期,中國製行動電源品牌 ROMOSS 羅馬仕也因安全疑慮召回逾 50 萬顆產品。更早前,韓國釜山航空亦曾傳出疑似行動電源自燃,導致機艙起火,凸顯行動電源對飛航安全構成的潛在風險。
根據中央社報導,今年 6 月 13 日,一班自鄭州起飛的上海航空班機上,一名旅客的行動電源突然冒煙,所幸機組人員與旅客即時處置,最終安全降落。
為因應相關風險,中國民航局近日發布緊急通知,明令禁止攜帶未經 3C 認證或已列入召回名單的行動電源登機。雖非針對單一品牌,卻反映監管機構正加強對高風險電子產品的控管。
但這也引發更根本的問題:擁有標章是否就代表真正的安全?
資料來源:中國民航網
事件回顧:品牌商該如何完善供應商的盡職調查?
根據 Anker 安克創新於官網發布的說明,此次事件起因於供應商使用了未經品牌方授權變更的原材料。該批次電芯在長期循環使用下,可能出現隔膜絕緣失效,進而導致過熱甚至起火風險。
這反映出品牌方對供應商製程掌握度不足,在原材料變更、製程細節與最終品質之間,缺乏足夠的透明度與即時連動。尤其在物料與製程環節未建立『綁定與核可機制』,一旦供應商私自調整用料或流程,品牌方將難以及時察覺與介入。
是否「看得見」、「管得好」每一個生產步驟?
對多數電子代工廠而言,生產規模龐大、產線複雜,各工站所執行的作業流程多且細,作業人員出現操作錯誤在所難免。而對現場管理者來說,也難以即時掌握每一個工站的細節,錯料、漏步、作業順序錯誤等問題往往只能事後追查。
這樣的挑戰對代工廠已經不小,對品牌廠更是如此。當品牌方缺乏一套可即時查看、可信任且自動化的品質管理系統時,對外部供應鏈的製程與品質也就難以深入掌握。
一旦出現瑕疵或異常,往往難以及時定位問題與控管風險。
解方:製程影像與 AI 視覺的實質助力
1. 實時管理:AI 視覺提升製程即時管理能力
PowerArena 的 HOP 人因作業平台結合 AI 視覺技術,具備即時辨識與分析能力,能全天候管理現場作業,判斷來料是否正確、操作是否依循 SOP、製程時間是否異常等。
當出現組裝角度偏差、料件錯用、步驟遺漏或工時過長等異常情況時,系統會即時發出警示,通知管理人員介入處理,協助現場迅速排除問題,防止不良品流入下一道工序。
在換線頻繁的生產環境中,HOP 可自動切換對應的 AI 模型,精準適配不同產品的料件與作業標準,確保生產過程持續穩定且一致。
透過這種「即時反應、即時修正」的機制,企業得以將品質管理從事後補救,推進為更主動、可控的製程管理與防錯機制。
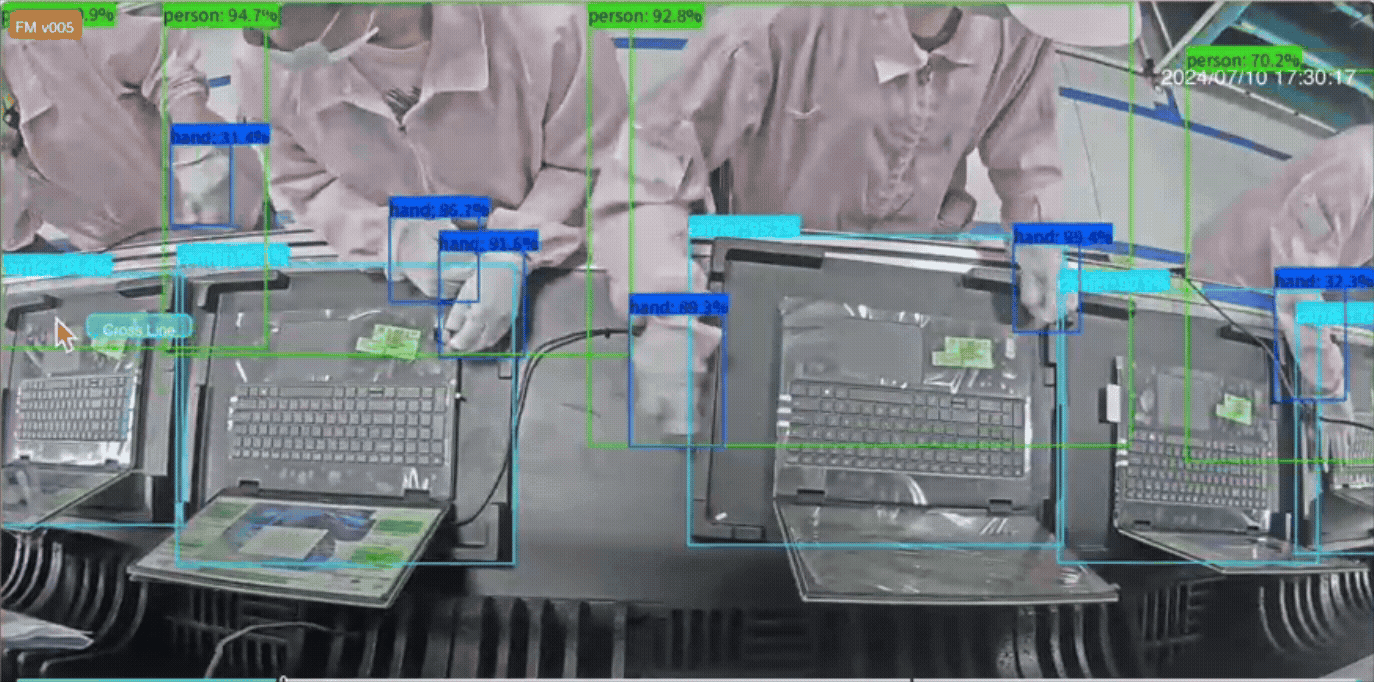
如離開工位或超過標準作業時間等情況,系統會自動標記並通報管理工班。影片來自 Compal 示範產線。
2. 製程影像紀錄:為每一項產品建立完善『生產履歷』
相較於傳統僅留下工單、報表或手寫備註,這些紀錄不僅可能遺漏關鍵資訊,也難以全面反映現場狀況。
PowerArena 的 HOP 人因作業平台自動化為每一件產品建立完整的「生產履歷」,將製程影像、作業時間、工站資訊與使用料件等關鍵資訊串接整合紀錄。
當日後需要追查肇因時,無需逐筆翻查資料或仰賴現場人員回報,管理者可直接調出對應時間、工站與影像畫面,迅速釐清問題成因,提升應變效率與準確性。
此外,系統支援跨部門、跨廠區甚至跨國查閱,讓各單位都能即時掌握一致的生產資訊,大幅提升管理透明度與溝通效率。
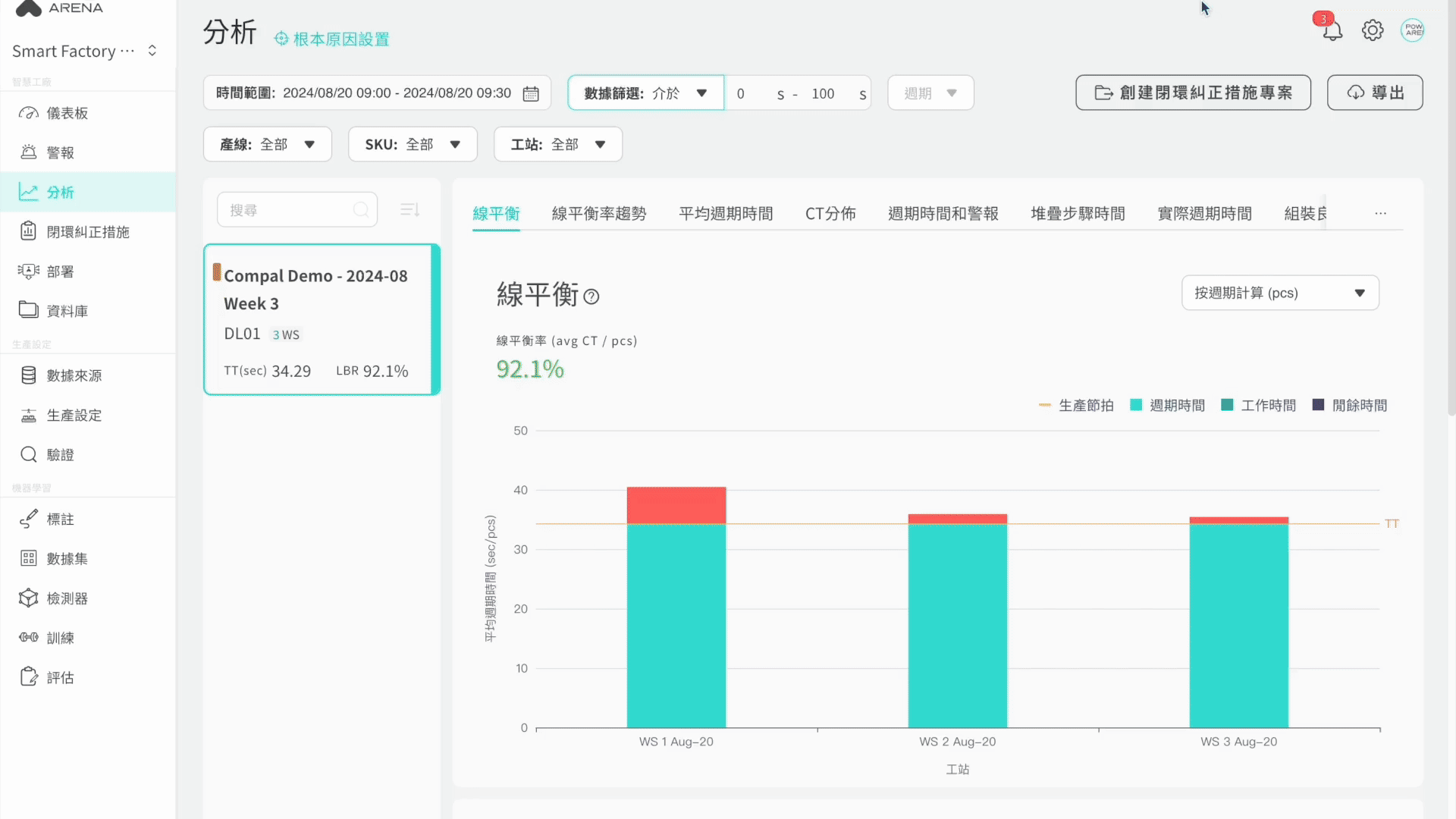
PowerArena HOP 人因作業平台透過生產影像記錄與分析,協助管理者自動辨別與定位肇因。影片來自 Compal 示範產線。
了解更多:關於製程的影像追蹤與自動化擷取
3. 精準追溯。召回範圍可控,風險管理有據可依
當產品發生異常、引發召回或安全爭議時,企業能否迅速釐清問題源頭,往往決定後續處理的效率與品牌信任的修復速度。
實務上,多數企業在面對產品風險時,常因無法定位問題來源,只能選擇「全面召回」。其主因往往是產品與實際生產工站或產線間缺乏綁定與資料對應,導致追溯困難。更嚴重的是,若無法確定瑕疵從哪一條產線、哪個時間點開始出現,瑕疵品可能持續流入市場,進一步擴大風險與品牌損失。
PowerArena 的 HOP 人因作業平台可在生產過程中自動將產品與工站資料綁定,當異常發生時,管理者能以產品批號、生產工站、生產時間任一資訊回調生產影像,獲得「影像 + 數據」的雙重佐證,有效鎖定影響範圍,確保召回落實並控制風險擴散。
結語:製程品管,是風險控制的起點,也是品牌韌性的基礎
對供應商而言,透過更自動化、數位化的系統強化製程品管,能在生產當下即排除瑕疵,並為每件產品建立完整的生產履歷,不僅有效降低返工與賠償風險,也有助於建立品牌客戶的信任與確保合規。
對品牌商而言,擁有一套可追溯、可信任、可取得的製程管理系統已成為必要條件,不僅提升對供應端的掌控力,更能實現生產過程的透明化,為品質把關提供更強的支撐。
在供應鏈日益複雜、品質與安全標準不斷提高的今天,從源頭落實製程透明與品質紀錄,不只是降低風險的手段,更是企業打造韌性與提升競爭力的關鍵所在。
想為您的電子產品產線建立可靠的生產履歷嗎?歡迎提出您的需求,由專人提供報價。
Table of Contents