Global Renowned ODM Improves Manual Line Management with HOP Digital Station
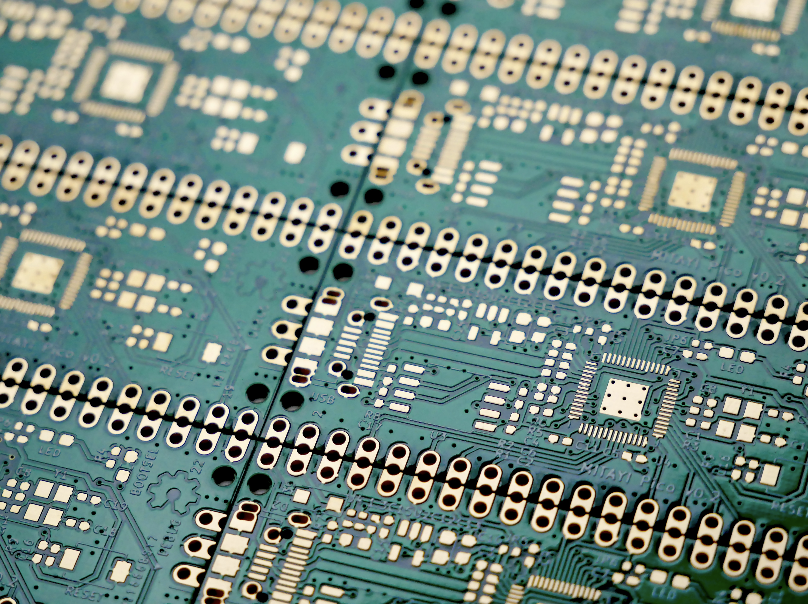
BACKGROUND
Global renowned ODM company focus on the production of high-value servers. The production line has 15 workstations. To ensure high product quality, precise control of each assembly step is important.
This company introduced PowerArena HOP “Digital Workstation” to optimize its manual assembly line management.
Pain Points and HOP Digital Station Solution
During busy production, workers sometimes accidentally scratch or dent the metal surface of servers with tools like screwdrivers, damaging products’ appearance.
Without a reliable tracking system, management struggles to pinpoint when and where issues occurred, making it difficult to resolve errors. In severe cases, this can impact shipments and cause significant losses.
Difficult to Track Workers’ Status. Lack of Reliable Data Support
Managers cannot monitor each worker’s status in real time, especially in labor-intensive production line. Traditional management lacks real-time and comprehensive production data for improvement. Managers find it hard to make decisions with concrete evidence.
Digitalized Manual Line
With HOP Digital Station, managers can view operations across all stations in real time. Managers can instantly check the dashboard to see if workers are at their stations and if any operational anomalies occurs.Managers can instantly check the dashboard to see if workers are at their stations and if any operational anomalies occurs.The system provides minute-by-minute updates for workers’ status.
Managers can stay fully informed on production conditions even when they are away from the line. This brings comprehensive, digitalized production management within reach.
Decline in Customer Trust in Product Quality
Without a clear production history, customers may question the overall quality when a single product issue occurs. It is harmful for company’s reputation and customer relationships. A lack of transparency makes it hard for customers to trust each stage of production.
Comprehensive Production History
HOP Digital Station automatically creates a complete production history for each product. Details in production are all recorded. This prevents data tampering and boosts management’s confidence in data. It improves decision-making reliability, ensuring greater transparency and a sense of security for both the company and its customers.
Unable to Track the Time and Location when Issues Occurred Pinpoint Issue Timing and Location
In traditional approach, managers often struggle to swiftly identify the exact time, location, or personnel responsible for surface damage incidents. This lack of visibility forces industrial engineers to invest extensive time and effort into tracking down issues—often a process akin to “finding a needle in a haystack.” Reliance on manual reports slows down investigations, dragging down production efficiency and impeding swift corrective action.
Unable to Track the Time and Location when Issues Occurred Pinpoint Issue Timing and Location
In traditional approach, managers often struggle to swiftly identify the exact time, location, or personnel responsible for surface damage incidents. This lack of visibility forces industrial engineers to invest extensive time and effort into tracking down issues—often a process akin to “finding a needle in a haystack.” Reliance on manual reports slows down investigations, dragging down production efficiency and impeding swift corrective action.
Track & Trace Anytime, Anywhere
Managers can access video footage at any time to quickly pinpoint the exact moment and location of an issue. Whether it’s scratches, dents, worker absences, or material buildup, managers can playback the video and quickly see what happened and identify the root cause. HOP Digital Station dramatically shorten resolution time and improve production line efficiency.
Results
Introducing HOP “Digital Station,” the company achieved the following goals:
About HOP Digital Station
HOP Digital Station boosts line transparency and enhances management efficiency. It reduces errors and improves production processes.
Product Features
1. MES System Integration
Digital Station seamlessly integrates with the production line MES system, providing complete data tracking and management mechanism.
2. Complete Production History with Video and Data
Combine video and production data to create detailed, easily reviewable records for each product.
3. Real-Time Tracking and Traceability
Track production status by time, SKU, or serial number, allowing precise root causes identification.
4. Transparent Management Interface
Real-time monitor for workstation, enabling managers adjust production strategies at anytime.
5. Digital Production Manual (Optional Extension)
Offer digital SOP guidance, which is displayed on tablets at each workstation to assistworkers in following standard procedures.
6. Workers Position Detection (Optional Extension)
Optional feature to detect whether worker are at their stations, with updates every minute.
HOP (Human Operation Platform)
PowerArena HOP is an AI-driven smart manufacturing solution. It visualizes production operations, providing real-time, transparent production information for labor-intensive lines. HOP features 24/7 data collection, AI visual analysis, and on-demand traceability. HOP consists of three levels of application: the first level, digital station, integrates diverse sensor data to establish image-based production records; the second level, AI line balancing, analyzes personnel operations, collects production data 24/7, and supports optimization engineering with precise cycle time and root cause analysis; the third level, AI Poka Yoke, provides real-time checks on SOP, detecting operational behavior during processes to prevent errors and improve yield.
HOP supports every decision you make and helps you achieve data ownership, paving a smoother route for your smart manufacturing journey.
About PowerArena
Leading the global manufacturing industry, PowerArena AI visual system was rated as the most competitive brand in manufacturing computer vision by Frost & Sullivan, one of the world’s largest management consulting firms, in 2022. Three out of the top five EMS (Electronics Manufacturing Services) companies globally have implemented PowerArena AI visual solutions to optimize production efficiency and enhance the value of “personnel” output. Founded by a former senior Google engineer, PowerArena operates service centers in Taiwan, the United States, Mexico, China, Hong Kong, and other locations.