Track & Trace. With HOP.
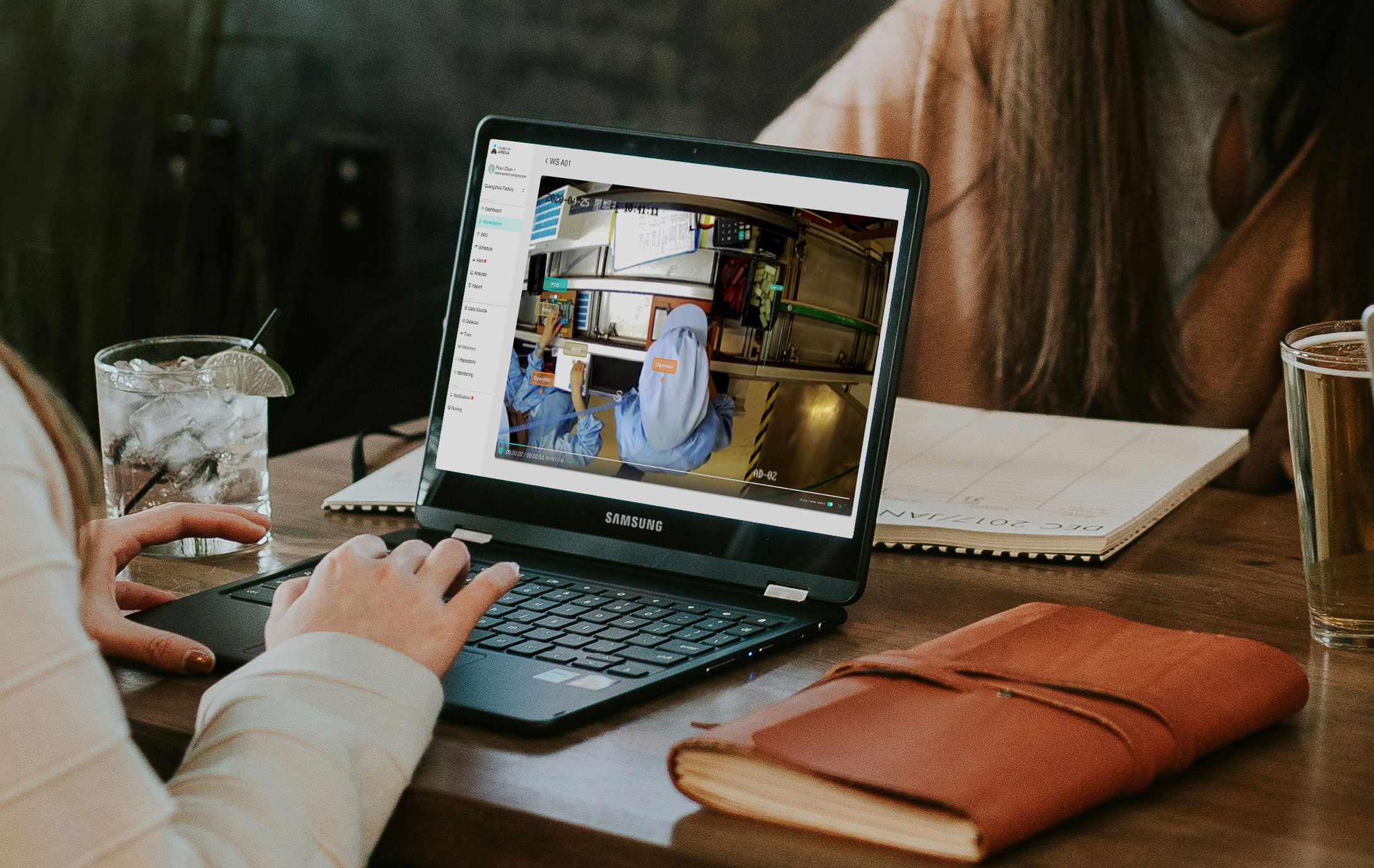
Actually…
Given the modern advances in tech of all fields, it wasn’t difficult to imagine a world where all of our products are manufactured by the most advanced automation robots in production. Truth is, an 83% of all the given products categories we use everyday are still heavily relied on the same manufacturing process 120 years ago—Manual assembly line.
Soon manufacturers around the world hunting for the next best solution to upgrade their existing process realizes, the invention and advances of technologies aren’t here to replace what’s already reliable and proven, rather to elevate. PowerArena believes in a world where technologies advances are to push the status quo forward, to promote a way of production where human operators can continuously pushing what they do best while with the assistance of artificial intelligence.
PowerArena’s Human Operation Platform (HOP) had been implemented into the most demanding electric manufacturing service production and stood the test of time while providing immense value. The number 1 request features from the manufacturing industry is to enable a complete production journey where you can track and trace to pinpoint even a single part of the final product to where it’s built. To identify and examine root cause and reenforce confidence to the final product knowing every steps of the productions is recorded in details. This is what we called, Track & Trace.
Track & Trace: Your production line supervision is now live with AI.
HOP’s Track & Trace collects your production line data using any tools available at your easiest convenience with full implementation to the current production management system.
Plug-then-Play
This enables HOP to a true plug-and-play system that uses existing IoT tools such as barcode scanners, electrical screw drivers, and video cameras to extract production info from each crucial work stations.
Live line supervision
With HOP’s Track & Trace video-backed data inputs, any durations of the assembly cycle can be identified in real-time, highlighting any missed steps, parts & materials supply issues and even the idle time of the front line workers.
Identify. Adjust. Elevate.
Line managers can now learn about their managed stations in real-time while it’s running. They can even monitor their production lead time knowing if it’s going to hit its UPH output all within their current shift.
Catch It At Its Core.
Real-time data points can enable industrial engineers to pinpoint irregularities down to the most granular level core of it’s root cause. IE then can use this data set to adjust production method, retrain & support operators, and prevent any ripple effects before it started. This also means if there’s product recall cause by potential flaws in product design or unit assembly, track & trace allows manufacturers to trace back to the very source of the problem and examine the process as a whole. More to that, during a problem dispute after initial process examination, track & trace also provide the full un-biased reflection of the production to base the judgement upon.
The applications of HOP’s Track & Trace can be endless. This translates into a more precise lead time calculation, higher confidence in forecast of production outputs, less slowdown in productions, a better trained and performed operators with full support of the Human Operation Platform.
The Playbook: How EMS industry uses Track & Trace
EMS. Trace to where it all went wrong.
The most crucial part of a EMS production line is rhythm. Every operators with their every steps at each single work stations all working harmonically.
A normal EMS produced unit can easily takes over hundreds of steps before it reached to the final product. And in average a single operator can handles up to 660 units in a single day shift. That is dozens of lines, hundreds of operators and thousands of work steps all going at a nonstop pace for only a few industrial engineers to oversee.
This creates:
- Delayed root cause analysis caused by imbalanced operators to supervisor ratio.
- Hidden causes of production irregularities.
- Misidentifying root cause due to fragmented production data points.
- Higher slowdown in production.
- Inaccurate lead time forecast.
HOP’s Track & Trace can help solve this problem by providing a complete overview of your production line down to each work steps with data points collected via off-the-shelf IoT devices such as barcode scanner, video cameras …etc.
Golden and then more: Boost in productivity in matured line
With implementation less than 2 months, HOP had boosted productivity up 18% in even the most matured line of the top 3 EMS provider of the world producing car electronics. This top manufacturer is also seeing value created in having fully digitized production line data sets, enabling them to uncover their own data gap and closing it with accurate AI analyzed data output.
Pioneers: Staying ahead of the curves
Another global top 5 EMS provider are also using PowerArena’s HOP as one of their flagship production plants initiatives for developing their future of manufacturing process. Within 3 years of partnership, PowerArena’s HOP solution is now live in over 3 regions of their factory sites around the world. Providing their top management real-time production overview and enabling executive decision making with deep integration of Track & Trace into their day-to-day production line. With AI implemented production line, it creates one of the most robust manufacturing process help them stay ahead of competitors that is still evaluating using AI to their offerings.
Production resume: A full production journey
Global top server manufacture are using HOP’s full integration of IoT tools to collect and built data points of their server production. HOP’s Track & Trace get to stick an unique identifier to each parts of their server assembly. Production line supervisors can now trace back to the very point where the parts is being worked on to fully examine the production process. They can then determine which action to be taken to future proof the issue, given it be retraining operators or to tweak the standard operation procedure. This unique yet essential ability helped this global top server manufacturer to achieve higher rate of product output yield and minimizing cost used to allocated for quality examination.
With benefits include:
- Uncover any hidden data gap in production
- Fully digitize production data set from work steps cycle time to production journey.
- Precise calculation on lead time forecast.
- Real-time monitoring of production to support immediate adjustments of assembly line.
- Fact based data to support streamlining production.
- Minimizing future re-training workers and potential production slowdown cause.
- Better allocation of management & operational cause.
About Us
About PowerArena
With world leading manufacturing AI vision system—Human Operation Platform, PowerArena was deemed the most strategically competitive brand by Frost & Sullivan in 2022. 60% of the global top 5 EMS providers now have HOP live in their factories across multiple continents. PowerArena is the most advanced manufacturing AI software company funded by ex-Googler and now with locations all around the world in North & Central Americas, Taiwan, Hong Kong and China.
HOP (Human Operation Platform)
Human Operation Platform is the industry leading AI powered manufacturing improvement solution that enables full potential for labor intensive production line.
HOP collects, analyze, and realize your production with plug and play IoT devices to offer real-time data points, creating a full transparent and reliable digitization of your factory.
HOP applications includes: 24/7 data collection with digital station. Track & Trace of a fully digitized production line. Accurately status overview of your production. Root cause analysis for actionable insights. In process quality control for the highest standard of production demand.