By Sursha Wu
前言
在智慧製造的浪潮下,大量企業已著手投入 AI 領域的應用
根據 2023 市場報告,美國過去五年在 AI 投資已達 2,900 億。而在導入 AI 後顯著提升利潤與降低成本方面,製造業表現第二名。
Source: IngestAI, The Global AI Investment Landscape: Trends, Players, and Opportunities
PowerArena HOP 人因作業平台,是專為製造業打造的智慧製造 AI 解決方案。
透過 AI 視覺技術,建構自動化產線管理,解決管理層在勞力密集產線中的管理痛點。
HOP 人因作業平台已成功應用於多個案例,導入後的案場均因 HOP 獲得了實際效益。
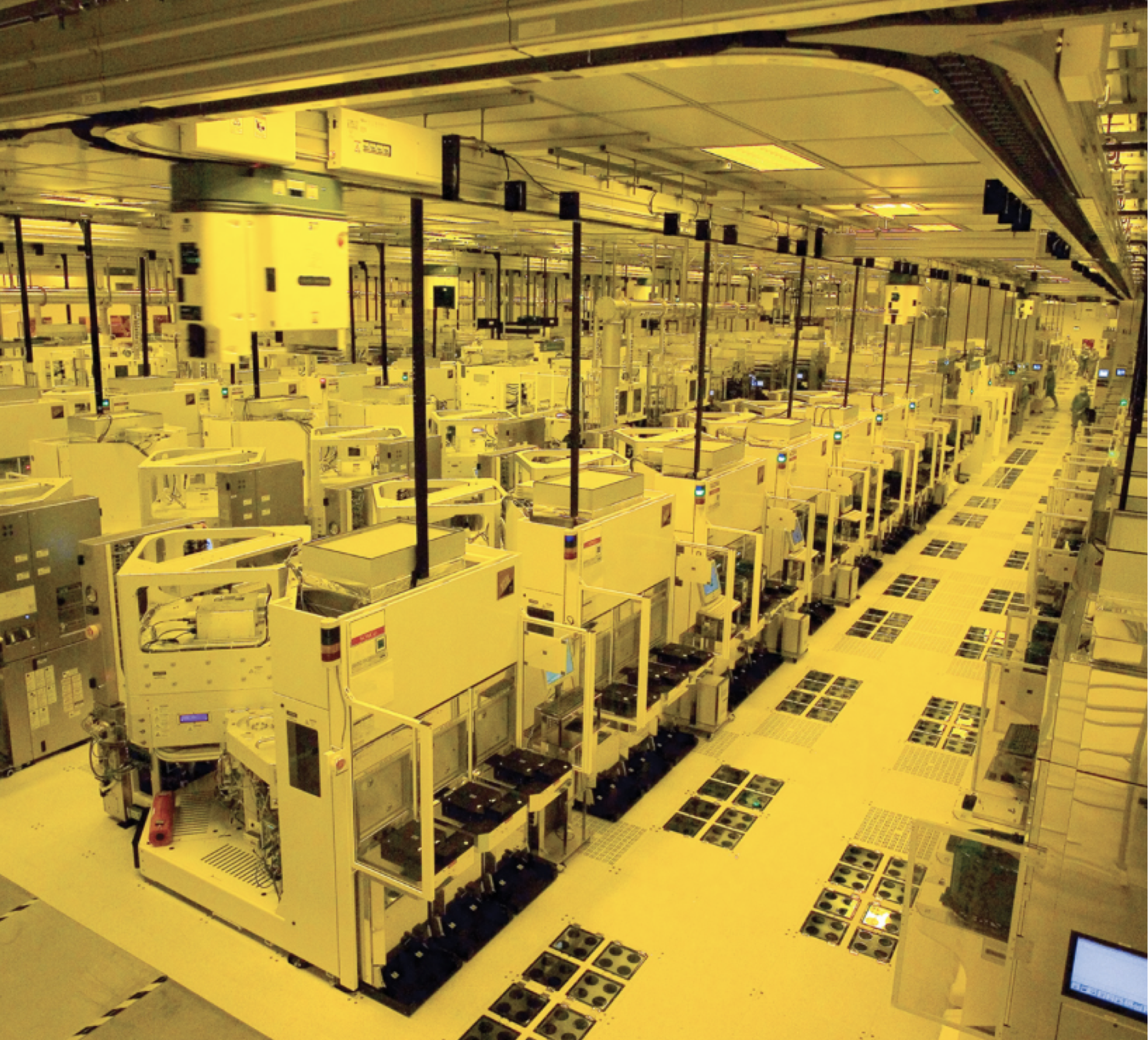
半導體工廠
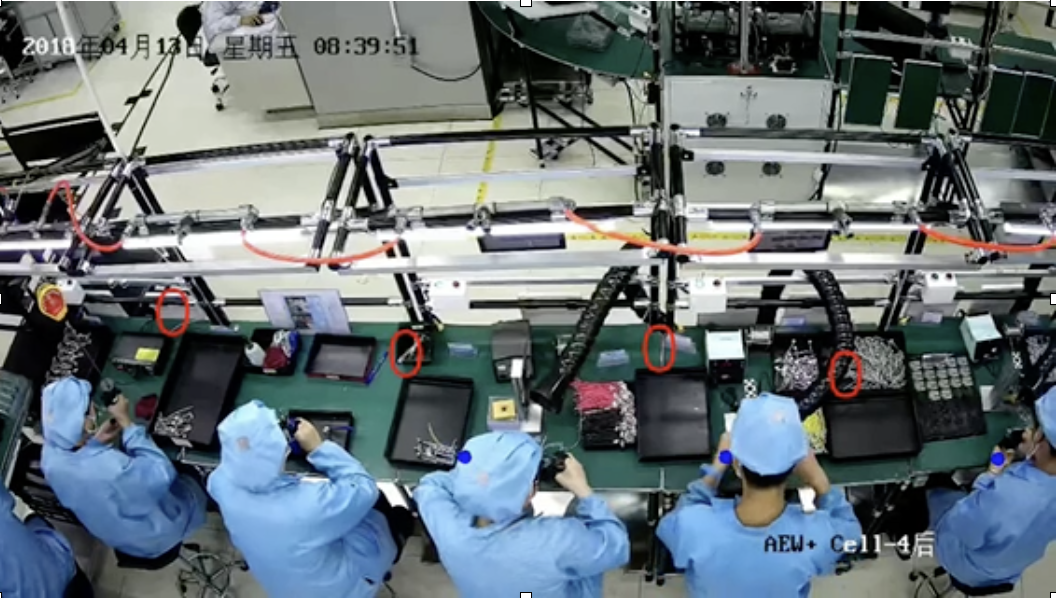
EMS 工廠
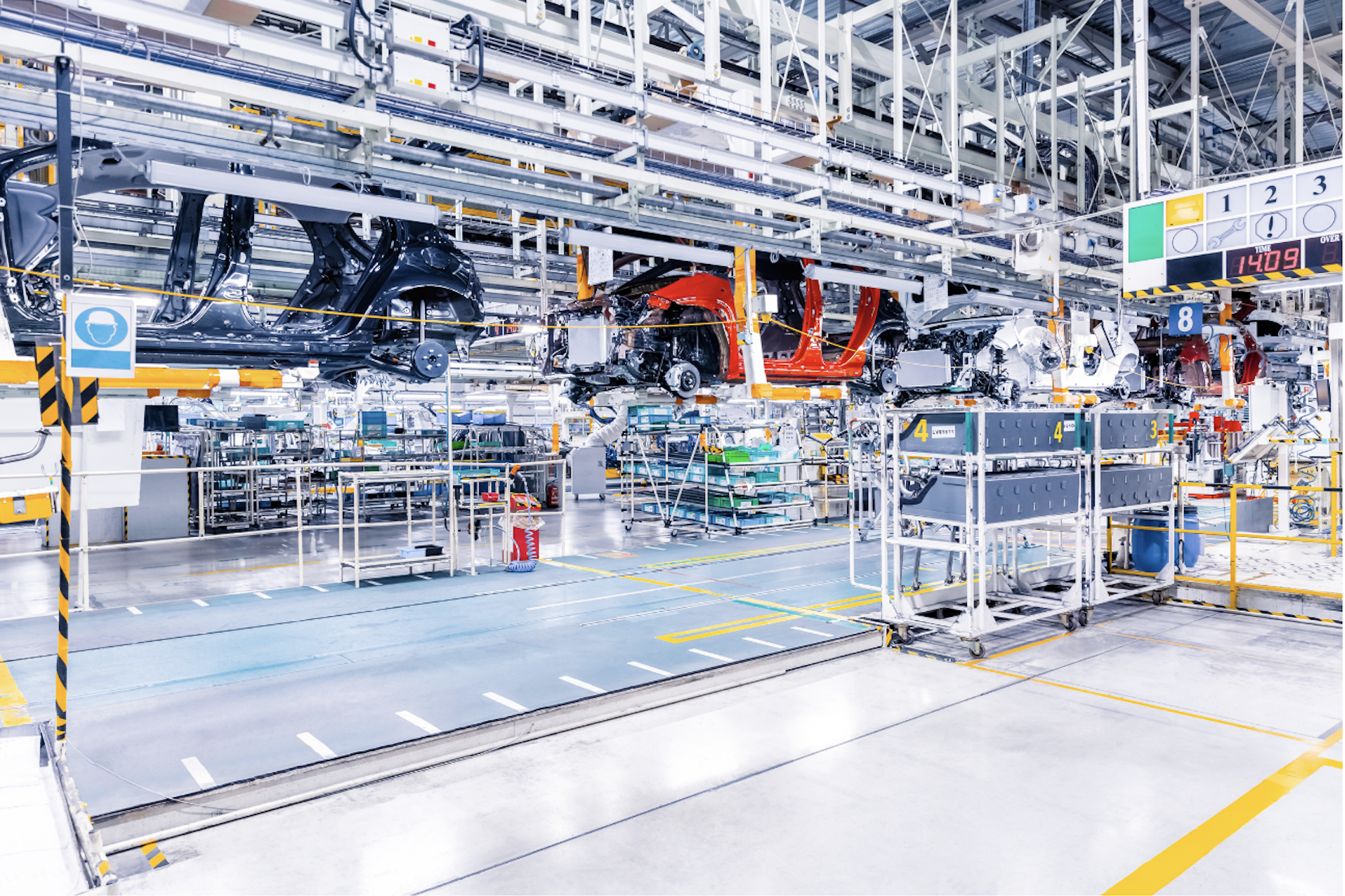
成車組裝工廠
本文會介紹 HOP 導入過程中的五個步驟。讓您更清楚地了解從決定導入 HOP 到落地實施後,會需要經歷的合作過程,以及 PowerArena 在其中所扮演的角色。
考慮導入 HOP 前的幾點注意事項
導入 HOP 之前,需要多方面的準備與規劃。
確立需要解決的問題
企業應首先回到產線,了解當前生產的瓶頸或痛點。可能是影響效率、品質或管理透明度的關鍵問題。確立好想要解決的目標,能讓我們更快知道 HOP 能如何協助產線優化。
具備基本標準化的作業模式
HOP 系統的核心是追蹤與記錄異常,而這需要基於標準化的 SOP 流程。我們建議工廠建立規範化的作業流程,為 AI 提供明確的分析框架。
預備搭建數位基礎建設
為滿足 HOP 的運行需求,企業需具備基本數位化基礎或願意投入相關資源,以利系統運行,例如:攝影機、網路架設及伺服器等設備建設。設備規格將根據產線需求有所不同,以確保系統在影像傳輸與資料運算中高效運行。
HOP 導入工作流程
不同於在手機上安裝軟體,在產線上導入 HOP 人因作業平台需要緊密合作與調整的過程,才能為產線創造最大的價值。
Step 1: 再次釐清作業痛點
我們觀察到,工廠在最初確認需求時,常常與真正影響效能的核心問題存在落差。
PowerArena 的專業團隊,致力於幫助客戶收斂思考路徑,剖析生產現況,找到核心痛點。
曾經發生的案例是,客戶希望利用 HOP 的 AI 視覺,協助偵測燈號是否亮起,以確保某個作業流程已被執行。然而,經過深入討論後,我們發現,真正的痛點並非燈號的亮起與否,而是需要確認該作業步驟是否被確實執行。
PowerArena 不僅擁有領先的 AI 技術,亦累積多年深入研究工廠作業的經驗,對生產流程有著深刻的理解。因此,導入的第一步並非匆忙按照客戶的需求直接執行,而是透過我們的專業諮詢,幫助客戶發覺產線的核心問題,進而共同討論出最適合的 HOP 切入方案。
Step 2: AI 模型認知場景
核心是讓 AI 模型充分了解產線的運作場景。
取決於不同的產線作業模式,所需的數據量可能會有所差異。
影像資料需要盡可能涵蓋所有可能的作業動作、人物、物體特徵。主要的目的是,讓 AI 能「看到」最足夠的場景資訊。
目前,HOP 具備基礎模型(fundamental model),已預先訓練識別如手部、人物、載具和印刷電路板(PCB)等基本元素。
若是屬於基礎模型已涵蓋的生產過程,就可以省去許多這部分訓練的時間。
Step 3: 協助產線標準化
在數據搜集完成後,PowerArena 會協助客戶再次釐清並定義作業標準,確保作業標準統一。
一個常見的情況是,許多產線管理層對實際生產狀況並不完全了解,這往往導致作業過程中存在「模稜兩可的標準」。
舉例來說,某產線的 SOP 規範要求:右手拿工具,左手拿零件。然而,從生產影像中我們發現,部分作業員是根據自己的習慣使用慣用手操作。此時,我們需要和產線管理者的合作,確認這種差異是否會影響生產效率或產品品質。如果會影響,就需要設置偵測;如果不會,則可能是 SOP 設計本身需要優化。
此階段的目標不僅是讓操作標準化,更是確保 SOP 的設計具有實際意義,排除不必要的追蹤因子。
對於 AI 模型而言,標準化的動作能提供更準確且有價值的數據,確保 AI 不會偵測到「無效異常」。此外,透過這個過程,管理層往往能更明白作業員在產線上的操作行為,而審視現有 SOP 的不足或不合理之處。
Step 4: 上線
完成 AI 模型訓練及產線標準化後,HOP 便可快速部署至生產環境。
對於基礎模型已涵蓋的需求,上線流程僅需 2 至 3 週,即可幫助管理者透過 Dashboard 執行生產數據的即時追蹤與分析。
在初期運行中,產線過去隱藏的大量生產問題會因 HOP 的導入而浮現,此時可能會需要再針對部分的生產步驟優化,排除無效變因。
針對這些情況,PowerArena 將持續提供專業支持,幫助客戶獲取最有價值的產線資訊。
Step 5: AI 模型微調與維護
對於 PowerArena 而言,我們的工作並不僅止於 HOP 系統的成功上線。AI 模型的持續效能關鍵在於定期的微調與維護,才能有效面對生產環境中可能出現的變化。
AI 模型的資料飄移(Data Drift)現象
在生產環境中,AI 模型的效能可能隨著時間出現波動。
這主要是由於資料飄移 (Data Drift) 現象引起的。資料飄移(Data Drift) 是指因**生產環境的變化,**使得模型的預測準確性下降。
例如,產線光線條件改變、設備位置挪動或工具折舊時,AI 模型的偵測會改變。或者,我們可以理解成,AI 模型會將這些細微的變化視為「新的生產過程」,所以出現無法正確辨識的情況。
不同於人類對「變化」能保有彈性的理解與適應,AI 模型需要透過數據更新來重新學習這些變化。
同時,為了保持模型的準確性,PowerArena 設計了維護機制,將資料飄移的影響程度將至最低:
- 信心度監測:持續監控模型信心度,及早偵測異常數據。
- 模型微調:根據新的數據分布進行調整,確保模型適應新的生產條件。
- 動態適應:目前 PowerArena 的 AI 模型已具備對光線、旋轉、平移等常見變化的適應能力,大幅減少因環境因素造成的誤差。
PowerArena 在導入 HOP 時的角色
在導入 HOP 的過程中,PowerArena 同時擔任 AI 視覺技術專家與智慧製造顧問的角色。
我們不僅擁有領先的 AI 技術,還累積了多年製造業導入與執行的經驗,對工廠管理和生產運作的細節有著深刻的理解。
PowerArena 提供的價值不僅限於技術層面,更在於幫助客戶快速定位產線的核心問題,並提供能切實助益生產流程的解決方案。我們認為,只有技術與實務相結合,才能真正為產線創造長遠的效益。
同時,因為多年專注於製造業的經驗,我們的團隊具備足夠的行業知識 (domain know-how),而 HOP 的 AI 模型也專為製造業運作設計。這樣的結合讓我們能顯著縮短導入時間,幫助客戶快速上線並取得成果。
HOP 為產線帶來的立即效益
HOP 徹底改變了過去依靠偏差樣本,來評估產線生產狀況的方式。
因為 HOP 對全面生產過程的數據蒐集與分析,管理者終於能夠真正「看見」完整的生產全貌,而不再依賴少量數據來推測整條產線的狀況。
導入 HOP 的過程中,管理者必須重新檢視生產流程,這往往讓他們發現許多過去未曾察覺的問題與細節,進一步加深對產線的理解。
透過 HOP,管理者能即時掌握每個工站的運行情況,無論是全局策略還是細節優化,都有清晰、可靠的數據作為支撐。這不僅幫助他們快速定位問題,還為優化產能、提升產品品質以及制定更精準的生產策略提供了堅實的基礎,徹底提升了整體生產效率和管理效能。