Looking to improve line balancing in your factory? This guide explains what line balancing is, why it is essential in lean manufacturing, and how AI, especially AI vision systems, can help detect bottlenecks, reduce idle time, and increase production efficiency. It also outlines practical steps and real-world examples to help you achieve balanced workflows using modern digital tools.
This blog is for:
- Production managers seeking to optimise shop floor efficiency
- Industrial engineers looking to implement smart line balancing techniques
- Operational leaders exploring AI-driven manufacturing improvements
- Continuous improvement teams focused on lean transformation
What is Line Balancing?
Struggling with Line Balancing in operation management?
Line balancing is the process of evenly distributing tasks across a production line so that each workstation operates in sync with takt time—the rate at which products must be completed to meet customer demand.
When a line is well-balanced, work flows continuously with minimal idle time, delays, or bottlenecks. Line balancing is a fundamental strategy in lean manufacturing that directly improves throughput, reduces waste, and maximises productivity.
In modern factories, AI-powered tools such as AI vision systems are transforming how manufacturers implement and maintain line balance by enabling real-time visibility, data tracking, and smart task reallocation.
Benefits of Production Line Balancing
Implementing line balancing in manufacturing offers numerous tangible benefits, including:
◎Prevent Bottlenecks
Balanced lines maintain consistent workflow, reducing delays caused by overloaded workstations and ensuring smoother operations.
◎Reduce Waiting Waste
Line balancing minimizes idle time for both machines and operators, ensuring efficient use of resources and reducing unnecessary downtime. For example, reassigning tasks between stations can eliminate waiting periods for workers or machines.
◎Minimize Inventory Waste
Balancing production lines helps reduce excess inventory and work-in-progress, freeing up capital and aligning production more closely with actual demand.
◎Meet Customer Demands Efficiently
By maintaining a balanced line, manufacturers can meet customer demand promptly, reducing lead times and improving overall satisfaction.
◎Increase Flexibility
A well-balanced line allows for quick adjustments to fluctuations in demand, ensuring that production can adapt efficiently to changing circumstances.
◎Boost Profit Margins
With optimized use of labor and equipment, line balancing reduces operational costs, maximizing productivity and profitability while minimizing waste.
How can you achieve line balancing? (5 Steps)
1.Calculate Takt Time
Determine takt time by dividing available working time by the rate of customer demand. This serves as the benchmark for your production line’s performance.
Takt Time=Customer Demand/Available Production Time
Example:
If you have 8 hours (or 480 minutes) available for production and the customer demand is 120 units, the takt time would be:
Takt Time=480 minutes/120 units=4 minutes per unit
2.Perform Time Study
Measure the cycle time of each task using stopwatches, IoT sensors, or AI vision. This reveals workload imbalances and shows where improvements are needed.
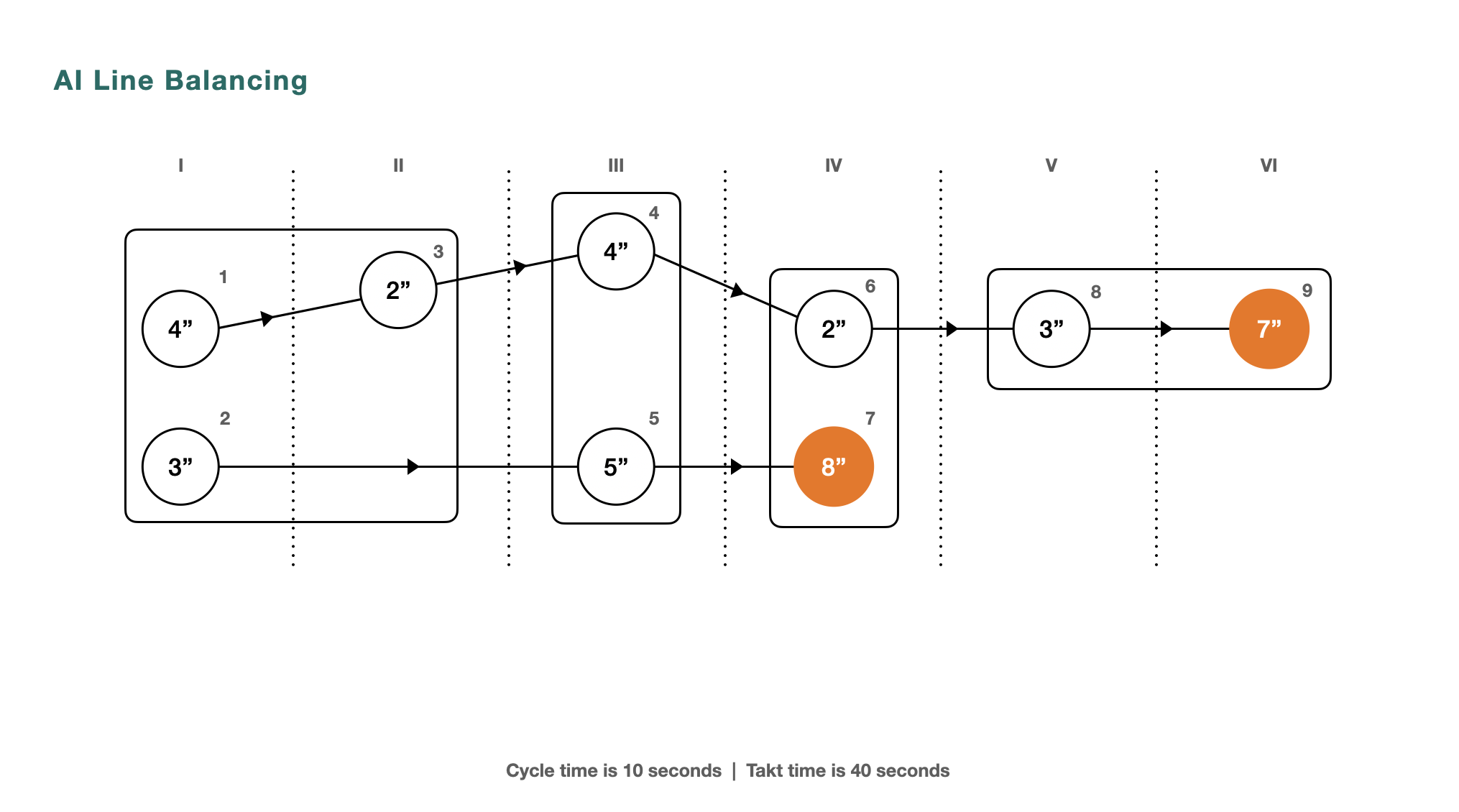
AI Line Balancing
This image shows a typical line balancing setup with tasks spread across six stations (I to VI), each labeled with time in seconds. Arrows indicate task flow and dependencies, while orange circles mark bottlenecks—tasks that take longer (8” and 7”).
Line balancing helps evenly distribute workloads to reduce idle time and delays. Even with parallel task paths, longer tasks like Task 7 can slow the entire line. A 10-second cycle time keeps operations in sync and aligned with the 40-second takt time to meet demand efficiently.
3.Identify Bottlenecks and Excess Capacity
Analyze your time study data to spot bottlenecks—stations that exceed takt time—and areas with excess capacity where tasks are completed too quickly.
4.Reallocate Resources
Restructure task assignments to better balance the line. Prioritise task sequence and operator capability. In manual lines, this may require re-training or SOP updates.
5.Implement Continuous Improvement
Use lean tools like 5S, Poka-yoke, and visual controls to continuously monitor and improve balance across shifts or product variants.
Want to see how AI vision transforms line balancing on the shop floor?
Optimize Your Line Balancing With AI Vision
AI vision systems are transforming how manufacturers maintain balanced production lines. Unlike manual methods, AI vision offers real-time data collection, automated analysis, and intelligent task reallocation. These capabilities allow factories to improve efficiency, detect bottlenecks early, and reduce idle time without changing line layout.
How AI Vision Enhances Line Balancing
- Real-time data tracking: AI vision captures live cycle time, operator activity, and machine usage from every workstation.
- Automatic bottleneck detection: When tasks exceed takt time or operators fall idle, the system flags delays immediately and highlights the root cause.
- Dynamic task reallocation: The system recommends task redistribution between stations to maintain flow and balance. This is especially useful when some stations are overloaded and others underused.
- Workstation behavior analysis: AI vision monitors operator motion and task precision to identify training needs or inefficiencies that affect throughput.
- Operational flexibility: The system adapts to takt time changes, schedule shifts, or product mix variations in real time—helping maintain balance under varying production conditions.
Key AI Vision Benefits on the Shop Floor

Key AI Vision Benefits on the Shop Floor
Case Study: How AI Vision Helped Balance the Line and Boost Output
A leading EMS factory in Southeast Asia faced ongoing issues with unbalanced workflows and hidden inefficiencies—until they adopted AI vision technology.
Without full-time monitoring, production managers had no clear view of where delays were happening. Operators frequently left workstations, tools malfunctioned, and upstream issues created unexpected idle time. The result? Lower productivity and limited visibility for improvement.
Inside This Case Study, You’ll Learn:
- How the factory uncovered 20% hidden idle time without adding sensors or new machines
- What caused frequent line interruptions—and how AI vision caught them in real time
- How a simple shift in task allocation led to a 5.2% UPH boost across the line
Conclusion
Effective line balancing is the foundation of a smooth, efficient production line—and AI vision is the key to mastering it.
PowerArena’s Human Operation Platform (HOP) helps manufacturers gain real-time visibility into human and machine operations, automatically detect bottlenecks, and rebalance tasks with data-backed precision.
By continuously tracking workstation activities and cycle times, HOP empowers production teams to reduce waste, improve UPH, and maintain optimal flow. The result: faster response to on-site issues, better use of manpower, and a more agile production line.
Want to see how AI vision transforms line balancing on the shop floor?
FAQs
Q1: What is line balancing, and why does it matter in manufacturing?
Line balancing is the process of distributing tasks evenly across all workstations to match takt time and ensure a smooth production flow. It helps eliminate bottlenecks, reduce idle time, and maximise resource efficiency. For manufacturers aiming to improve throughput and reduce costs, effective line balancing is a core lean strategy.
Q2: How can I identify if my production line is unbalanced?
An unbalanced line often shows signs like operator idle time, queues of semi-finished products, missed takt time, or inconsistent output. Time studies, manual observation, or digital tools like AI vision systems can help pinpoint imbalances and inefficiencies in real time.
Global Top 5 EMS Company Balanced its Line with AI Vision
Q3: What are the main methods to improve line balancing?
Common line balancing methods include:
- Conducting time and motion studies
- Calculating takt time accurately
- Reallocating tasks based on cycle time
- Introducing standardised work and visual controlsDigital solutions like AI-powered platforms can continuously monitor task durations and suggest adjustments dynamically.
Q4: Can AI technology really help with line balancing?
Yes.
AI vision systems can track each workstation’s performance, monitor operator movements, and collect real-time cycle time data. These insights help managers identify bottlenecks immediately, adjust workloads, and maintain line balance without relying on manual checks.
Q5: What’s the first step to start improving line balancing with AI?
Start by defining your takt time and collecting current cycle time data for each station. Then, implement an AI vision line balancing system that can visualise task flows, track operator actions, and suggest real-time reassignments to balance workloads effectively. No major layout changes are needed—just better visibility and data-driven decisions.
Table of Contents